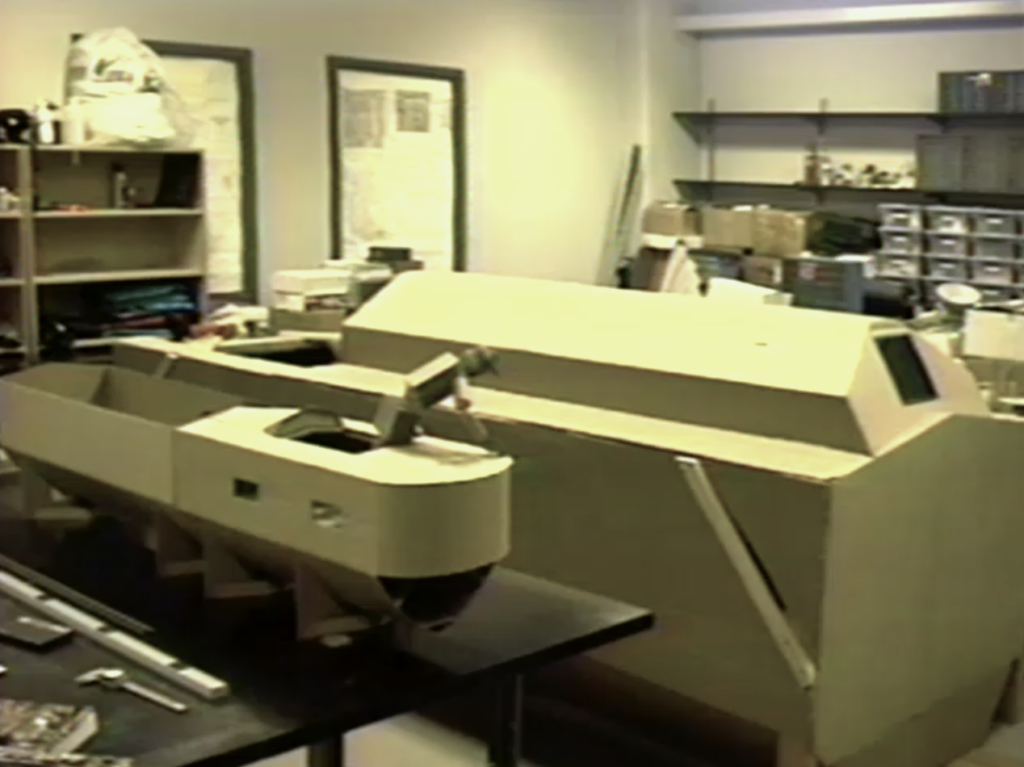
Microship Updates – September 1993
Things were moving quickly, with setting up the new UCSD Lab and getting to know students arriving for Fall Quarter. As with the past July and August, we are keeping the archives tidier by grouping these frequent early posts into mong-long collections. Video from this period is in the archives, and will be embedded in the text.
Microship Status 09/01/93
The project continues… I’ve been immersed today in cardboard and hot glue, building mini-Steve, a 25% cardboard replica of myself (rather squarish and clunky, but correctly scaled to help in model visualization). I’m not going through this again, though: I’m ordering a 16.5″ (25% of 5’6″) wooden mannequin from an art supply store to simulate a hypothetical traveling companion. I’ll call her the wood nymph…
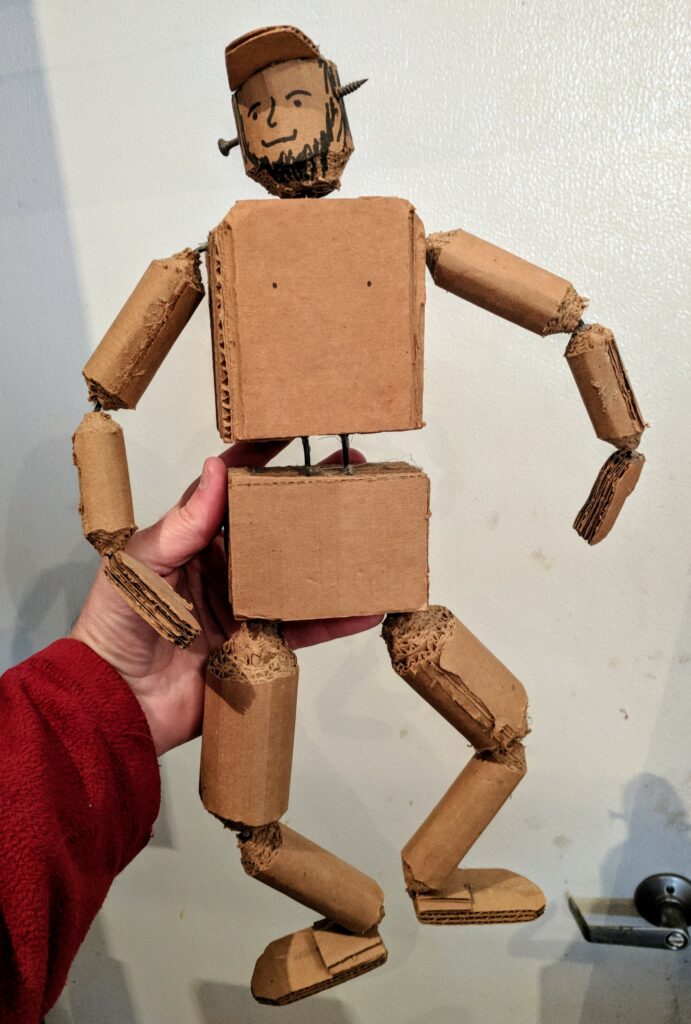
Anyway, mini-Steve is already helping reality-check the section of the model that is complete, and will become more and more useful as decks and the main cockpit area are completed. He’s currently perched on the afterdeck with his feet in the crew seat, jauntily watching the world drift by…
Good telcon today with GeoQuery (I’m a beta site for 4.0). I put them in touch with ComGrafix in Florida (Mac charting software), and the intent is to have them jointly develop a completely integrated charting and geographic database management system, linked to GPS data and various maritime resource lists in addition to my own people files. They are receptive to supporting a student project, so this may become a major top-level Mac application.
Off tomorrow to look at a trimaran for sale, browse Seabreeze books, and possibly visit Corsair Marine. I’m also preparing to buy a sextant and learn celestial navigation.
As an aid to physical design of the boat, I thought it might be useful to list the functions that must be supported. As I play with the models, I’ll try to put them through all these paces and make sure there are no major gotchas. I did this with the bike, too, but it was relatively trivial since most physical tasks involved only the land-based use of on-bike facilities. This is different, since there will not necessarily be places to stand other than those designed into the boat. In no particular order (and not necessarily all at sea), the actions are:
- Writing, email, and other computer work
- Use of navigation charts (in addition to on-screen work)
- Cooking and food consumption
- Sleeping under deck
- Sleeping in tent mode (atop solar panels)
- Laundry
- Head use, pump-out, and manual cleaning
- Showering and personal hygiene
- Electronics maintenance
- Beaching
- Safely deploying kayaks while at sea or at anchor
- Swim platform
- Access to all stowed gear
- Close personal interaction with companion
- Ham radio, including any special antenna deployment
- Anchoring
- Sunbathing and relaxation
- Heavy-weather survival
- Hull access for fiberglass repair
- Securing system for unattended storage or mooring
- Slip and dock access
- Sailing
- JATO mode (emergency electric thrust)
- Voluntary dismasting for clearance
- Conversion to narrow-beam mode while underway
- Pedaling (both crew)
- Bike deployment for land use
- Changing clothes
- Fishing
- “Feeding the fish”
- Watch changes (crew to main helm; SKR to cabin)
- Going forward safely
- Accommodating guests
- Calling for help
- Stowing all lines and loose gear
- Trailering
- Cold weather survival
- Hot weather ventilation
Doubtless there are more, but as I get lost in the details of cardboard models, it’s useful to force a series of what-ifs based on the above list.
LITERATURE RECEIVED:
Electric Boat Association May/June 93 newsletter and membership info
Ray Electric Outboard motor information
Tidefinder tide/current computer literature
Polhemus 3D position sensor literature
Everfair catalog, primarily Fourwinds wind generator systems, other marine electronics
MetaFormal Systems literature on MacNavigator, very thorough HyperCard nav softare for Mac
Moonlight Products — more night vision scopes
Celestaire — detailed catalog of sextants and celestial navigation tools… including Astra IIIB for $395
Video: Corsair F-27 trimaran, one hour
System Three epoxy starter kit with accompanying how-to literature
Microship Status 09/02/93
I made another pilgrimage today — to the high-density marine-supply region around Shelter Island. The original purpose of the trip was to go see a $9,000 trimaran for sale down in Chula Vista… but it turned out to be a plywood clunker, junk really, so I spent a few hours exploring. In the process I made some excellent contacts in the marine electronics biz, played with an Astra sextant, and spent about $80 in the nautical bookstore.
While doing all that, it suddenly occurred to me that I may be able to parlay some of my high-tech nomadic experience into project funding. The yachting world is full of people who long to disconnect and be free, yet still need to stay in effective communication. This has become one of my specialties over the years, so I’m going to invest in a couple of small ads in Latitude 38 and Santana to see if a bit of consulting might pay off. I have no interest in hands-on work on other peoples’ boats — my own will keep me quite busy enough — but I could generate custom reports of suitable products and system configurations on the basis of interviews about the intended application. It’s a wealthy clientele, and I’ve never seen anyone advertise a similar consulting service, so it may work. Or it may bomb… many business ideas do. In any case, it’s easy enough to try with virtually no investment, so we’ll see!
Hobnobbing among the yacht brokers, chandleries, and specialty stores is useful, even though my boat is on a smaller scale. Seeing how other people have solved problems helps me take steps to avoid similar ones, and I’m noticing a gradual evolution of the design based on all this reading and learning. It seems a slow phase, but I’d rather be methodical now and do it right than have to make a major hack to fix something critical.
One issue that is surfacing is the shape of the amas, or kayak outriggers. Since a trimaran should fly the windward hull when reaching, the optimal ama shape is not just a function of displacement hydrodynamics. We also have to consider what happens when it returns rapidly to the water — too flat and it will generate major shock to the structure. I’m concerned that the standard kayak shape may be suboptimal in this regard, but rate their modularity highly. Could be yet another design trade-off.
Also, examination of a Corsair F27 today suggests taking a close look at their ama-deployment design, which occurs in a different plane from the “parallelogram” method I initially postulated. More on this as I explore it further.
That’s it for now — I’m on a deadline crunch with the Internet World article (that will also run in SunWorld Japan). Back to it…..
LITERATURE RECEIVED
(plenty of new reading material today — between Seabreeze Nautical Bookstore and visits to the Shelter Island marine businesses…):
Maiden Voyage – book about solo circumnavigation by then-18-year-old Tania Aebi
The Spirit of Rose-Noelle – book about trimaran capsize and 119 days adrift, by John Glennie and Jane Phare
1993 Southern California Boaters Directory
California Boating (cruising guide)
1993 Mariners World Marine Directory
The Cruising Multihull – book by Chris White detailing trimaran design
Sailing the Farm, a Survival Guide to Homesteading on the Ocean – book by Ken Neumeyer about living at sea
Beachcruising and Coastal Camping – book by Ida Little and Michael Walsh
SeaLand portable toilet literature
Autohelm instrument catalog (autopilots, instruments, navigation)
Pioneer Stereo marine products literature
Cruising World magazine (Sept 93)
Harken yacht equipment catalog (cleats, blocks, winches, etc)
Ronstan catalog (similar product line to Harken)
Microship Status 09/03/93
A quickie today — Friday night, still working on articles, and the world of productivity is grinding to a halt as everyone becomes unavailable for a 3-day weekend.
I have a Microship-model deadline: Sept 16. That’s the day Robb Walker of Nelson/Marek will visit the lab to discuss the requirements in more detail and see what miracles I’ll want him to perform. Worked on it some more this evening… made 6 stands to hold it up, and cut the main tube of the recumbent from a piece of pine. I’m getting into a major wall-staring phase as I try to integrate dozens of conflicting issues into a 10′ cockpit section (now further complicated by things learned from The Cruising Multihull book).
I spoke today with Current Designs, the kayak builder in British Columbia. While he hasn’t explicitly said he would donate boats (Expeditions or maybe Libra doubles), he does seem very enthusiastic about the project and told me they’re entering their quiet season which lasts until about November. So the time is now to define the spec and make a proposal… he’s sending literature which will help me determine the optimal placement of crossmembers and hopefully avoid any need for a custom deck plan.
One of the issues related to that is hatch design. Trimaran floats are subjected to very heavy abuse including submarining through waves, which in any kind of interesting conditions will quickly strip anything loose from a kayak deck — including the typical fabric cockpit cover. I’ll have to either redo the hatches to allow yacht-scale square hatches, or have Mark Plastics (Hesperia) fashion custom removable plexiglass covers that can then be gasketed over the curved coamings with stock hardware. The kayak main cockpits will also need automatic electric bilge pumps.
Drainage is another problem… depending on bouyancy calculations and the PPI figures (pounds of added load per inch of immersion), the heights of cockpit and sleeping cabin floors are going to have to be adjusted to allow self-bailing. If not, every time a big wave hits with open hatches it will cost a lot of work and/or power…
(I don’t mean to give the impression that I’m heading offshore into blue water, but I’d rather agonize now over worst-case scenarios and then find myself well prepared than design the boat for gentle waterways and then drown on my first tentative bay crossing. Thinking always in terms of heavy wind and concomitant waves will make this a much more robust boat, though it’s maddening right now.)
I’m toying with the idea of a hard top over the cockpit, with easily removable vinyl windows. While this sounds rather ugly, it will provide shade and basic weather protection in what is otherwise a rather open boat, sliding hatch covers notwithstanding. It is yet unclear whether there will be any way to “go below” in the main cockpit — the bike imposes tough constraints (and no, I’m not fully wedded to its inclusion just yet, though it does convenienty define the inflexible parameters of the human pedaling envelope, a level of functionality upon which I stubbornly insist).
Anyway, the hard top would cover most of the 4′ hull width, and to allow passage forward the non-slip walkways would move outboard to the extended wheel wells — which could actually run most of the length of the boat, bounded by lifelines and stanchions. Sounding more like a yacht all the time. Maybe I should just find $60,000 and buy an F-27 .
Speaking of the F-27, by the way, I’m seriously considering stealing its aka-deployment scheme instead of my initial parallelogram method wherein the kayaks stay in the water and sweep sternward. It’s a bit hard to explain in text, but basically the crossbeams are on wonderfully articulated arms when vertical, but settle into very strong wells when deployed, requiring only a single bolt as a hold-down. I’ll show you the video if you want to see how this works (TJ saw it today).
Other design issues currently affecting my thinking are the required buoyancy of the outrigger kayaks, which should nominally support the full boat to provide an effective transverse static righting moment after being heeled to its point of maximum stability. Such considerations affect kayak volume, overall beam, and even the length-to-beam ratio or “fineness” (which should be a minimum of 8:1 on the center hull according to White, though present design at 28′ x 4′ is 7:1). The crossbeam should also support at least 20 times the overall boat weight to handle worst-case conditions. Given kayaks of known dimensions (18’10” LOA, 22.25″ beam, and 118.6 gallon volume — or 21’8″, 30″, and 184.4 gal if I elect to use doubles instead), we have to work backward to set constraints on center hull parameters, which are themselves driven in the opposite direction by liveability requirements… then tying it all together with crossbeams at a known distance apart but yet-unknown length and downward curve (which cannot be known until bouyancy calculations show the difference in freeboard between vaka and amas…). Hell, after all this, the electronics will be a SNAP.
Microship Status 09/09/93
Overload! As model deadline nears, I have been realizing just how much has to be decided yet… it’s going to take a succession of late nights (my most productive hours) to finish this.
Because of the difficulty of visualizing body interface in quarter-scale (even with mini-Steve), I decided to make an actual-size mockup of the cockpit section (a 10′ hull segment). The idea is a 4x4x10 foot frame of 2×4 lumber, with cardboard hull and deck surfaces. Inside, the bike will be supported at the right hight (about 2′ off the bilge) on a wood platform.
The first step in such an undertaking is a job for… Obtainium Man! Donning my special obtainium suit, I crept out last night under cover of darkness and performed asset-relocation on the requisite scrap lumber. Tonight I’ve been converting Nickel-Cadmium chemical reactions into sufficient torque to drive drywall screws, cobbling together a decidedly ugly frame amidst a growing sea of sawdust (an unfamiliar sight in the Microwave Lab, I bet). Next is the bike support…
The reason for all this is that knee clearance, console geometry, hatch placement, stowage areas, and the FEEL of the thing need to be done with visceral involvement. First comment after frame completion: this thing is HUGE. It’s not really a kayak anymore, and we’re surely well over 1,000 pounds. This forces me to reconsider pedaling, and I’m concerned about beaching. At some point in this continuum, it becomes a yacht… at which time, it would make more sense to simply acquire a yacht and outfit it appropriately. Something seems distinctly wrong about that approach, so we need to take a hard look at scale and perhaps push things back in the kayak direction by narrowing the hull 15-20%. Nudging the figures in the OTHER direction, however, are livability, adequate storage, and safety in rough conditions. We’ll see. Soon. Somehow.
Meanwhile… I find myself juggling trade-offs that I didn’t even know existed. Good advice from the net continues to arrive (I’ve been posting in rec.boats), covering bouyancy calculations, prop design, sight reduction, rudder placement, chemical toilets, strip planking, and more. Great stuff. I’ll discuss it here as the issues surface for real.
The books I bought last week are now under my belt (or somewhere), another excellent source of input during this critical and somewhat frustrating phase. I’m looking forward to reporting on real hardware progress in this forum soon! Somewhere in the middle of all this, I need to write the BEHEMOTH Technical Manual, keep up with monthly magazine columns and occasional speaking gigs, and launch this little nomadic connectivity consulting business with possible addition of an OmniTRACS email service…
I hate being finite.
LITERATURE RECEIVED:
Electric Boat Assoc Newsletter Aug/Sept 93
Multihulls Magazine May/June 93
Scientific Atlanta literature on mobile satellite voice and data terminals
Book: The Monthly Sky Guide (Ridpath/Tirion) for aid in identifying celestial objects
New Age Yacht Restoration flyer on electric motors.
Microship Status 09/15/93
Ah yes, this is another one of those “daily” reports… thought I’d better bring you up to date now, since this weekend I’m leaving for a one-week road trip via the Mothership, hauling BEHEMOTH to San Jose for a speaking gig (Mobile World Expo). Given the expected overload of email, paper mail, and new people upon my return, this series of postings may be quiet for a while!
Tomorrow (Thursday) is the meeting with Robb Walker of Nelson/Marek — he’s coming to the lab to see my cockpit mockup and models, and to brainstorm the actual boat design. This should be a significant event, and will hopefully start the process of defining the hull shape and getting us moving toward construction of the physical substrate. I’ve been preparing for this for the past week, and my lab is now dominated by a 10-foot-long, 4-foot-wide, 3-foot-tall cardboard mockup, built onto the wood frame I told you about in the last issue (but shortened a foot in height — what sounded good on paper was too big in reality). I can now sit in it, go below to crawl through the access tunnel to all the electronics and equipment stowage areas, flip up the keyboard desk, and otherwise have fun pretending I’m on the high seas (which is even more fun than playing with the mini-Steve doll). With all the developments lately, I want to summarize the current state of the design for you.
There are now three hull segments, not four:
V1, the 10′ bow module, is only accessible through a deck hatch. Since this is the region most likely to suffer a hull breach, I want it well-sealed from the rest of the boat. This is the place for wet things and long-term storage, and includes: sail stowage chain locker for the anchor through-hull water intake for desalinator and processing environmental data collection flotation compartments many antennas on deck bowsprit with front rudder and trailer hitch mast-supported shower head (over hatch) (not compatible with roller-furling; details unclear) folding bicycle stowage (Attila Dahon) Long-term supply storage
V2 is the 10′ cockpit module, and the region of greatest complexity (the mast is at the boundary between V1 and V2). The center section of this module from cockpit forward is about a foot higher than deck level, providing headroom below in the access tunnel — a 6-foot-long, 2-foot-wide space that is walled by sealed equipment and storage bays on both sides and terminated forward by a fold-down chart table and fold-up stool (a secure workspace for electronics, foul-weather writing, etc). This cuddy cabin, of sorts, carries windows and lights, and topsides provides a surface for sail control lines that don’t impede the walkways.
The cockpit itself is an interesting place — the seat bottom folds up to provide access to the head (most sensibly located here, given all the possible usage patterns), and the back folds down to allow passage through the V2-V3 bulkhead to the crew module. A hinged desktop flips up and carries waterproof keyboard and pointing device, and a variety of panels and storage hatches satisfies all the needs for manual bilge pump and valves, comm gear, system monitor panel, rudder controls, PFD and emergency gear, and so on. For security and foul-weather protection, a hard top matching the cuddy dimensions slides forward from its stowage atop the V3 cuddy, locking into place above the console. Somehow, I’ll fit a retractible bimini to this for sun/weather protection while underway. (You should wander by the lab and see the mockup to make sense of this — reducing it to text is a bit difficult.) I won’t list all the items in the cockpit module, since they comprise virtually all of the Microship’s on-board systems and personal gear stowage.
V3 is the 10′ crew module, the aft-most segment of the main hull. Access is via either bulkhead hatch or crew cockpit — which can be locked via a relatively planar sliding cover that retracts sternward into a slightly elevated deck envelope as on the J-24. When open, this provides comfortable seating for my companion (with a bimini as above); when closed, this is a 4×7 foot bed with adequate storage below and behind. Also, the aft-most part of this will be the cooking area (think “camping,” not “shipboard galley” — remember, this started out as a kayak…). In bed mode, the seat folds down and its cushions join the plane of the sleeping surface (this is demonstrated in the quarter-scale model). Other parts of this surface fold up for access to a 1-foot deep storage well under the entire bed, and along the stern are wall lockers.
It occurs to me that a worthwhile safety feature is a place to cower out of the weather if the boat is inverted (see below for thoughts on that) — PERHAPS the underside of the bed can serve this purpose if I’m willing to forego segmentation for stowage convenience.
The cockpit module (V2) cannot accommodate much in the way of deck clutter like antennas — the boom/foot will sweep across fairly low. That leaves all remaining skyhooks, the radar tower, and stern pulpit to populate the deck of V3, with a no-skid walkway bounded by safety lines on stanchions running the full length of the boat. Note that the solar panels match the V2 segment perfectly, and will join seamlessly with fenders that cover the still-mysterious wheels to yield a very wide and comfortable deck space when underway.
I’ve been in contact with Current Designs and a local designer about the kayak choices, and we’re leaning toward Libra doubles (1570-pound displacement) on both sides for buoyancy and space. An interesting twist is that I might be able to pedal-power them (notice no mention of the bike in the center hull description above). I’ll keep you posted as this develops.
The issue of capsize is one that concerns every multihuller, and this is no exception as it grows to the point where I can’t easily flip it with my body weight. I concocted the following scenario, which admittedly depends on a few key working components but could save me in a life-threatening capsize:
- Microship is flipped by rogue wave. Pilot panics, recovers, and clings to inverted craft fighting off grim visions of sinking, sharks, and breakup on nearby rocky lee shore.
- Pilot recovers composure and begins recovery process by jettisoning the highly buoyant solar panels (tied to lines) and flooding one of the kayaks by opening valves. Microship begins to tilt.
- Crew labors at a manual air pump that inflates a bladder attached to masthead. Boat continues to rotate, and is now stable on its side in the water with one kayak straight down and the other up in the air.
- Pilot and crew remove and stow sails to minimize weight and water-catching, then clamber up to airborne kayak, attach something like a hiking strap, and lean far out over water. Hopefully, boat rights itself, dumping both people in the drink unless they’re quick.
- Pilot closes flooding valves of other kayak and starts bilge pumps (manual and electric). Solar panels are recovered and reattached.
A couple of things complicate this: First, we must assume that the conditions that caused the capsize in the first place are still in effect, making the whole exercise extremely difficult or even impossible. Also, it depends upon pumps, hoses, bladders, and other high-tech gizmos that could fail and may be difficult to operate when hypothermia, fear, and even injury are involved. This is one of the costs of increasing the size of the Microship to support more technology and enhanced livability… there are ways to call for help, and ways to right it with power-boat assistance, but if I’m ever crazy enough to be alone Out There this is one of the risks I will face. Hence the two special safety measures — detachable seaworthy kayaks to serve as life rafts, and a dry place to pass the hours out of the weather with the boat inverted.
In happier news, Ron Fellman came by the lab yesterday and we fell to talking about the pointing device for the Mac (I guess you know from my message to this group Friday that Apple is sponsoring two machines, and has offered the assistance of Mike Clark — designer of ADB and the gorilla-proof Mac used by Koko). I pulled out an XY Force-Sensing Resistor array donated to the bike project by Interlink and we started discussing using it as a waterproof mouse. I observed that since it measures applied force as well as X-Y position, we could translate force into cursor velocity, and with that he grew quite enthusiastic and took the unit with him to begin interfacing it with a 68HC11. This could be an ideal solution to the boat’s mouse, and certainly has product potential… I’m looking forward to seeing how intuitive it can be as a pointer. Torque joysticks, which are the only waterproof pointing devices I know of, have an incredibly uncomfortable feel — this would provide the twin pleasures of tactile displacement and intuitive velocity control.
OK, this is a long one and I should get back to the design… I’ll try to report on the Nelson/Marek meeting before heading north for the speaking gig. Cheers from the lab!
LITERATURE RECEIVED
GeoQuery Beta 4.0B1
Tons o’ magazines from the base office; too many to list (73, Mobile Product News, QST, catalogs, etc.)
SEA Inmarsat terminal literature — only $7,000 for Standard-C; small antenna.
Colby demo video for video transmission over cellular phone, POTS, or 56K links.
Angelwing sail literature (inflatable sails with improved airfoil shape).
Landfall Navigation, extensive catalog of nav gear and charts (more pricey than Celestaire but large selection and good reference value).
Navlink brochure computer-assisted DOS navigation software.
A pile of material from the San Diego computer show, again too much to list and not all that relevant. One new sponsor there, by the way — Nada-Chair, an excellent lower-back support via straps to the knees. TJ saw it today and wants one too.
Microship Status 09/27/93
Back from a week on the road — both energized and exhausted. The focus of the trip was the Mobile World Expo in San Jose, where I displayed BEHEMOTH for two days while meeting with sponsors new and old, cavorting with friends various, selling books, learning about the latest developments in wireless and pen computing, and doing the Media Dance (including German TV). All this was bracketed by a succession of visits between here and there, including an evening with my new major contact at Apple, a jazz concert, numerous dinners, hikes in the mountains, telescope play, and more. In short, my usual method of making one week feel like three — as close as we can get to life extension!
That provided lots of new input on the boat, of course, but first, here are a few paragraphs written as an unfinished status report ten days ago:
Excellent meeting with Robb Walker of Nelson/Marek Yacht Design! He was pleased with the models, but a bit startled at how much the machine has grown in size since our first meeting about a month ago. The emerging tradeoff pits comfort and seaworthiness at one extreme against agility and “adventure” on the other. To help clarify my own thinking, I should try to define an operational specification:
The Microship must be small enough to easily portage and navigate through tiny rivulets, work well under human power, provide comfortable sleeping accommodations for two as well as a fully-stocked laboratory, be seaworthy under rough conditions, possess high WQ, zip across the water like the wind, and be virtually unbreakable.
Obviously, it’s impossible to check all those boxes… so what we have encountered is the age-old struggle between comfort and light weight. Security versus freedom.
I wrote that, left it in the unifinished mail queue, then had a road trip. Now I’d like to briefly update you on developments since.
First, as you know, Apple has become a Microship project sponsor. I spent a night at the home of Mike Clark in Glendale — he designed ADB, the gorilla-proof Mac used by Koko, and countless other things. Amazingly creative guy, and he’s part of the Vivarium Project (Learning Concepts Group). I now have a Mac IIFX in the lab, running AutoCAD Release 12. Of course, I don’t know how to USE AutoCAD yet, but at least the tools are in place. I’ll probably be getting a 180C PowerBook to hack into the console, and there should be quite a bit of technical support. As Apple’s interface-device expert, he’s also very interested in seeing how the Interlink FSR pointing device that Ron is working on will shape up — they’ve never tried it.
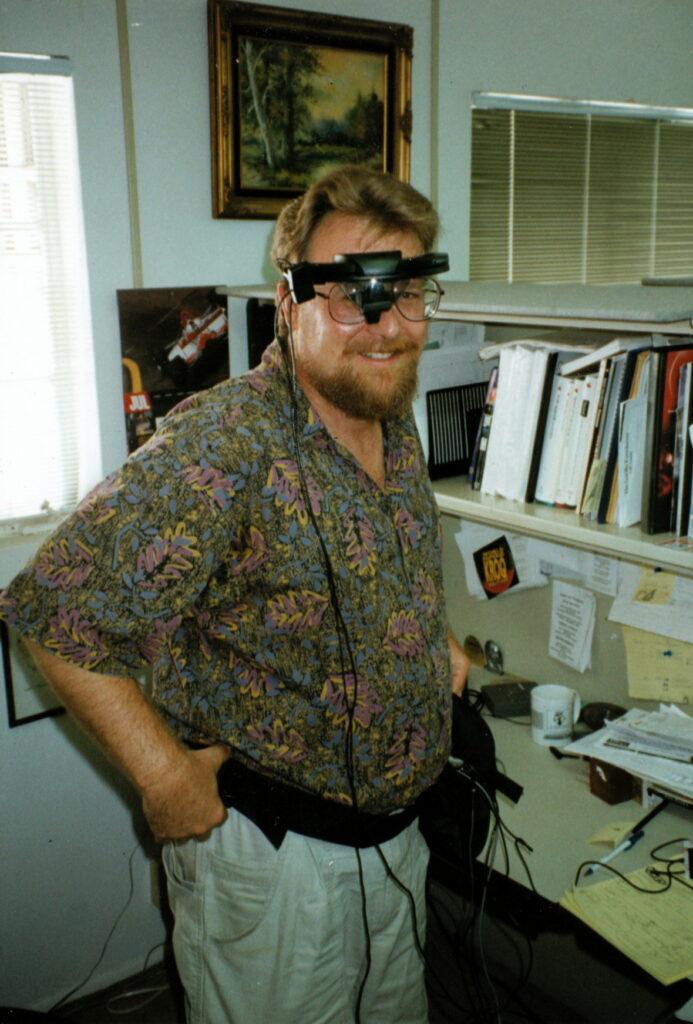
In the OTHER personal computing camp, there’s a fair chance of Compaq getting involved. I met them at the show and interest is strong… it’s added to the list of proposals that I don’t have time to write . There are quite a number of interesting DOS and Windows apps, and this would be a good way to include them in the system while also adding development bandwidth.
While at Mike’s house, I also had the pleasure of meeting Alec Brooks and Graham Gyatt of AeroVironment. Alec is distinguished for his development of the record-setting Flying Fish II human-powered hydrofoil, and Graham is launching a 100-foot long solar-powered flying wing. The company’s real work these days is developing the GM electric car, so we all had plenty to talk about… and Alec offered help with hydrodynamics and propeller design!
Dean Anderson from AT&T faxed a long document detailing Kurt Hughes’ “cylinder molding” method for skinny boat hulls. This may make MUCH more sense (and be significantly faster production) than the strip-composite method heretofore considered, and I’m now studying the literature to see if it can be applied. Again, the net comes through! This was a result of my rec.boats discussions.
The briefcase and notebook are full of business cards and comments about other people and companies… more as they develop. At the moment, I’m in recovery mode, with a daunting post tradeshow TO-DO list. More as I catch up with interrupt requests and noise reduction…
LITERATURE RECEIVED:
A pile of Mobile World tradeshow material from vendors various, including conference proceedings.
West System technical manual (epoxy)
Kurt Hughes article on Cylinder Molding technique
Canon still-video system literature
Trimble GPS literature
Microship Status 09/29/93
Wow… three months of these reports already! Once we get the new UCSD ftp site established for all the story archives, we’ll have to add the monthly collected files of these… required reading for newcomers and a good source of detail for Nomadness Notes and the inevitable book.
The past two days have included very little hands-on work, with the exception of AutoCAD and GeoQuery installation in the new Macintosh (including some education on the former courtesy of TJ). I also published a new UCSD help flyer, which will be handed out to interested parties during a BEHEMOTH show-n-tell Monday noonish at the Price Center (helping to promote my Wednesday evening ASME gig in CSB-001). We tried to do it today — late night last night finishing the flyer, up early to get the printing done, haul bike out to freight elevator…… which was out of order.
But there has been a major increment in the materials learning curve! I mentioned the cylinder-molding technique in this series a couple of days ago; yesterday I went to a composites conference at the La Jolla Marriott and spent an hour with Jeff Bootz of Nida-Core, Maury Shepherd of Film Technology, and Mark Livesay of Sunrez. What an interesting group…
Basically, Nida-Core is a polypropylene honeycomb structural material that is obviously perfect for the solar panels on the Microship (forget foam core!). It will be cooler, due to both radiation and convection within the cells, it won’t delaminate from crushing, and it has immense strength-to-weight ratio. I have some samples in the lab if you’re interested… I just need to get the allowable deflection specs on the solar cells, choose a thickness based on worst-case impact (my body falling from the deck and landing on my rump, probably), then design the longitudinal web structure that will impart ultimate stiffness and also support the hinge.
For the other composite work, the combination of Quick Draw vacuum bag resin transfer molding using Micro Channel films and UV-cured epoxy that can be drawn into the part by the vacuum pump — with virtually infinite pot life until hitting it with ultraviolet light — greatly simplifies the whole composite layup process. We have found the tools! I have samples of these products in the lab as well, if you’re interested — also contact info on the companies involved.
That’s it for tonight… fried!
LITERATURE RECEIVED:
Film Technology flyer on vacuum bag films
“Ten Years of Light-Curing in UP Resins” by Claus Thiele of BASF
Latest issues of PC Laptop, Portable Computing, Pen, and Mobile Office magazines
Compaq computer literature
You must be logged in to post a comment.