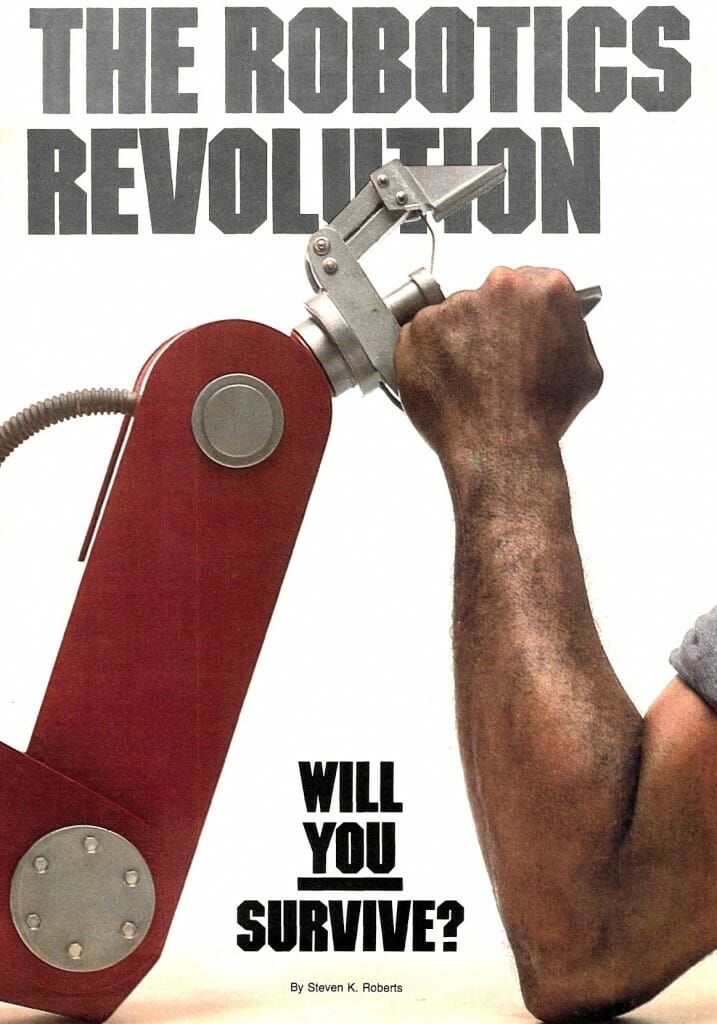
The Robotics Revolution – Mechanix Illustrated
During my years of freelance writing before embarking on a life of technomadic adventure, my favorite mode of travel involved going to industry and academic conferences and trade shows, then writing about them for a variety of markets. Often this involved hobnobbing with those developing new technologies and then slanting my article towards those who would likely be affected by them. This one is a good example… I spent a few days at the ROBOTS VI conference in Detroit, then wrote about it for Mechanix Illustrated. This was a good transition for me anyway… I had been writing almost exclusively for computer and electronics magazines, and it was time to start branching out a bit.
by Steven K. Roberts
Mechanix Illustrated
September, 1982
Robots — capable of two to three times the efficiency of flesh-and-blood workers — threaten to displace large numbers of people from jobs. Humans may prevail, but, strangely, the result might be mass unemployment, anyway.
IF YOU EVER want to get a spirited conversation going, just wander into an employee lunchroom somewhere in Detroit and start singing the praises of industrial robots. After you pick yourself up off the floor, you’ll probably become embroiled in a bitter dispute over worker displacement, Japanese auto imports, productivity and union contract terms.
There are two problems that make this issue of robot-aided manufacturing a complex and emotional one. First, the machines do indeed represent a threat to workers whose jobs they can accomplish with two to three times the efficiency. Second, there is a prevailing image of robots as so-called mechanical men that are bent on taking over society. Even at the recent robotics conference in Detroit, a couple of exhibitors saw fit to further advance this notion by using androids as crowd pleasers — an event which, of course, received national television coverage.
Like it or not, robots are arriving in large numbers on the doorstep of American industry. According to Norman L. Naidish of Revlon, Inc., “Robots could replace one million workers in the U.S. in the hard-goods and electrical industries by applying the technology in use today… Currently, about 5,000 robots are in use in the U.S., or about 0.3 percent of the potential.”
This is not part of some dark design to force workers onto the streets; it’s simply a result of the need to compete effectively in the world market. With Japan and many European nations running well ahead of the United States in productivity increases (Germany showed a 4 percent increase last year alone, while the U.S. has man- aged only .01 percent in the last six years), we are faced with the need to clean up our act or fall hopelessly behind. For some industries — like automobile manufacturing — it may be too late already.
Accomplishing the dramatic productivity increases that will enable us to survive is not a simple task. American industry is heavily burdened by a variety of problems: management structures that often penalize innovation; complex relationships with unions; public relations problems; and a dwindling supply of research and development capital. This is hardly an ideal climate for wholesale revision of established methods.
But there is little choice. It has been estimated that the cost of operating the average industrial robot is close to $6 per hour, compared to about $16 per hour for a typical plant employee. If the robot offers greater dependability, speed and efficiency — leading to reduced inventory requirements and a generally tighter-run ship — then those basic $10-per-hour savings are increased even further.
But this is not a line of reasoning likely to meet with the approval of an assembly-line worker who is being replaced with a computer-controlled arm having an arc welder for a hand. What’s needed through all this is a healthy understanding of the long-term implications of robot use, including its effect on production workers. As Thomas L. Weekley noted in a 1979 UAW position paper on robotics: “If workers perceive robots, or technology generally, to be the cause of unemployment or loss of income, they will no longer have a cooperative and receptive stance toward technology introduced by their employers.”
A SHORT HISTORY
One of the key features of human intelligence (at least as we humans see it) is the ability to create and use tools. This phenomenon has a long and colorful history, beginning with the fossil records from Rift Valley residents of two million years ago and continuing with increasing vigor to this day.
When the industrial revolution rolled around, there was considerable development of tools that would automate the manufacturing process. Not only did these allow faster and more efficient production, but they also gave companies closer control over quality, scheduling and so on. We know that dehumanizing factory conditions ensued, but in theory the use of automation was a good thing.
Even in factories full of specialized manufacturing equipment there still exist a number of 3-D jobs — those that are dirty, dangerous or difficult, not to mention the ones that are dull or dehumanizing. Nobody likes grueling labor, and the pay scales demanded by those doomed to perform it are high.
There’s nothing revolutionary about the idea of using machines to take care of some of these unpleasant jobs; for decades, specialized equipment has handled everything from surface grinding to part sorting. These forms of automation have displaced thousands of workers, but somehow it never became much of an issue. Why? Because the machines were very specialized. Adaptability on the part of a machine, however, is something that competes too closely with human talents.
An industrial robot briskly going about its business is sometimes a disquieting sight for people who have never seen one before. A car body is moved into position by a conveyor system, and a steel arm — with shoulder, elbow, wrist and hand — springs into action. Pausing only long enough to fire off spot-welds at intervals of a few inches, it works its way quickly around the door with the deliberate precision of a spider at work on her web. It is difficult to observe such a sight without feeling that the machine possesses intelligence — and that it is treading rather heavily on sacred ground once walked only by mankind.
This is, of course, quite untrue. The robot, while giving a convincing display of dexterity and planning, is actually nothing more than a blind, deaf, mute, numb, immobile output device for an uninspired computer that is performing a step-by-step sequence of simple instructions. If it has any senses at all — such as “feeling” it has bumped into something — they are primitive; if it has any adaptability to changes in the task, it is at a very low level. A human can select all the ¼-in. bolts from a bin of miscellaneous hardware with hardly a conscious thought, but even the most sophisticated of vision- equipped industrial robots runs into serious difficulty with such a task. It will be a number of years yet before a robot will be adaptable enough to react appropriately to unexpected events and the complexity of a typical production line.
Despite all these limitations, however, robots offer a tremendous advantage over the special-purpose equipment traditionally used in factories. Where most of the in-place production equipment is dedicated to some specialized task (and must be replaced or extensively re-worked to accommodate changes in a product line), robots are general- purpose devices and need only be taught the new or modified job. Many existing robot systems, in fact, can be computer-led through a task such as spray painting, welding or parts handling — after which they can repeat the operation tirelessly for months.
It is this sort of thing that raises the worker displacement issue. Clearly, a robot that is competent enough to replace a human or two and operate with minimal supervision represents a significant threat to the labor force. But this is counterbalanced to some extent by the increase in productivity — something that benefits everybody, not just company management.
THE REAL PAYOFF
Talk of increased industrial productivity sounds, to many people, like a rather lofty and abstract goal that has little to do with the labor market. But take a look at what happens when two hypothetical companies adopt opposite approaches to the robotics issue:
The Alpha Company and The Beta Company are competing firms engaged in the manufacture of gizmos. They have been around for 30 years or so and have historically shared about 85 percent of the domestic gizmo market. Lately, however, some low-cost, high-performance Japanese models have started carving out a substantial chunk of the U.S. market, and Alpha and Beta officials are worried.
To make matters worse, both companies are involved in labor disputes with the UGW (United Gizmo Workers) and have, during the last year, reported record losses to their stockholders.
Alpha management decides that the only way to avoid certain death is to drastically increase productivity, whatever the cost. They perform time/motion analyses, inventory analyses and efficiency studies, and quickly determine that their long-established way of manufacturing gizmos is, quite simply, outmoded. Alpha engineers start attending robotics trade shows, eventually producing a plan for a totally revitalized production operation.
Beta management takes a different approach. Even though company brass are aware of computer-aided design and manufacturing technology (CAD/CAM), they are guilty of short-term thinking: It is safer, from a manager’s standpoint, to maintain things the way they are rather than to institute a bold new initiative that might fail. Robots are discussed in countless committees, and the buck is tossed endlessly.
The UGW, bent on protecting its members from job loss, threatens Alpha Company with a walkout if it doesn’t agree to provide retraining for displaced workers and to share the profits from new technology with the union. The lawyers work on all that, while a trial robot work “cell” is installed and demonstrated.
Beta Company plods along, blaming the production line for its problems and losing market share.
In about a year, Alpha Company has completely revamped its production line with the latest in robotics technology and quickly begins reaping the benefits of more efficient manufacturing: lower personnel costs; reduced floor space requirements; increased safety; lower workmen’s compensation expense; reduced work-in-progress inventories and so on. Then the interesting effect begins to occur. Alpha Company is becoming so productive that it can lower the price of gizmos, compete more effectively with the Japanese, expand its operation and hire more workers!
Rather than fade away, as did the other domestic gizmo manufacturer, Alpha Company regained its health by applying new technology and becoming more efficient. Beta Company finally died, after selling off subsidiaries, laying off workers and trying unsuccessfully to obtain a government subsidy.
The lesson here is obvious, but the problem it creates involves the acceptance of harsh short-term problems in order to realize long-term benefits. This runs counter to the thinking of much of our industry and becomes a particularly painful issue when the number of workers on a payroll has to be reduced. Even if the very survival of the American gizmo industry depends upon the large-scale use of robotics, it is going to be quite difficult to actually bring it about.
ROBOT TECHNOLOGY
It is quickly becoming clear that industrial robots are the technology of choice for boosting the productivity of American industry, especially now that over 4,000 of them are proving themselves in full-time, profitable use. (It is a bit disquieting, by the way, to observe that Japan currently has over 10,000 in operation and is producing around 7,500 more each year — five times the output of U.S. robot makers.)
To be useful in a manufacturing context, robots must possess certain key features. By definition, they are basically programmable manipulators, capable of moving a piece of tooling (the hand) to any location within a defined operating space (known as the work envelope). There are endless variations on this theme, ranging from pick-and-place units designed for very simple parts handling to highly articulated arms with as many as seven degrees of freedom (the ability to rotate the wrist, flex the elbow, etc.). The cost varies accordingly, and is also affected by varying capacities for speed, precision and trainability.
The foundation of all this, however, is not the robot’s ability to move its tooling to any point in the work envelope, but the underlying intelligence that guides its motion. It is most correct, in fact, to think of a robot as a computer that happens to have an arm.
But computers are useless without programs, and the robots that will survive in this industry are the ones that can be easily trained to perform different tasks. There are a number of units on the market that offer impressive mechanical specifications, yet require considerable technical effort on the part of the customer when it comes to fitting them to a newly changed production operation. This is hardly acceptable, since any company turning to robots is probably interested in flexibility.
There are three primary methods of teaching robots. The first, which is simplest for the machine but relatively demanding for the human, requires the programming of specific steps: open elbow 62 degrees; rotate wrist clockwise 31.5 degrees; close hand; etc. This is cumbersome and is quickly falling into disuse.
The second method involves taking the robot through the intended path while the system is in the learn mode. Some models require that commands be explicitly entered via a small keyboard; others actually allow the operator to grab the robot’s tooling and lead it physically through the job to be performed. In either case, the operator is relieved of the need to understand the innards of the robot system in depth.
Third, and relatively avant-garde, is the integration of a robot with a CAD/CAM system. This permits the entire task to be simulated on a graphic display, while the computer calculates the most efficient paths, integrates the action of all the robot’s joints to produce smooth and well-planned movement and corrects for out-of-range joint rotation.
At some point in the evolution of robot sophistication, however, we run into a problem. Without senses — sight, touch and so on — a robot’s adaptability to its environment is severely limited. You could walk up to a machine briskly assembling automobile alternators, for example, wait for an appropriate moment, then swipe all the parts. The robot wouldn’t miss a beat: It would just assemble air.
Such an image seems absurd to humans who constantly adapt their actions to physical reality. But it suggests what is perhaps the most complex problem of all in the development of successful robot systems: creating useful senses.
At the robotics conference in Detroit, there were hundreds of units on display, all busily performing demonstrations for the record-breaking crowd. But close observation revealed the machines’ fundamental stupidity: Almost all of them were blindly following a stored sequence of steps. If the flow of parts stopped, or if the pincers failed to pick something up, the machines would continue with the operation without correcting the problem. Most practical robots, of course, incorporate primitive sensors that prevent damage in the case of a jam or out-or-range operation, but only a few can adapt themselves to minor variations in the task.
Picking parts out of a bin is surprisingly difficult. Following a complex joint with an arc welder calls for more than technology now has to offer. Recognizing flaws in workpieces, reattempting a failed operation, adapting to variations — all call for the implementation of senses and the computational power to process the information.
Although there are a number of impressive machine vision systems on the market, it is impossible to separate vision from intelligence. Computers, alas, are still so primitive that even a simple task such as recognizing a face requires a minute or more of processing time — even then, the answer is only of marginal certainty. We have a long way to go before truly adaptable and intelligent machines start making their presence felt in the workplace.
All of which brings us back to an earlier point: Along with the quite valid concerns of worker displacement by robots, there is a vague, popular uneasiness arising from a fear that these things are more than just machines. The marketing departments of systems manufacturers freely throw around terms like “smart terminal” and “intelligent system,” even though the objects in question haven’t the intellectual power of a two-year-old child. The news is premature.
This technology is indeed revolutionary. But today’s robots are not the androids of Star Wars — merely the flexible outgrowths of traditional industrial control equipment.
Worker displacement? It’s inevitable. But the law of the jungle will prevail. Alpha Company will survive and grow; Beta Company will perish. Some of Beta’s ex-employees will go to work for Alpha. The robots will do the dirty, dull, dangerous and difficult work. And people (the most valuable commodity of all) will be put to work on tasks that require their intelligence—if they have been adequately trained in this newest of growth industries. After all, somebody has to build, transport, install, program, teach and maintain all these robots.
2014 Follow-up
The story keeps unfolding, 32 years later. And more, with an AI twist, in 2017.
You must be logged in to post a comment.