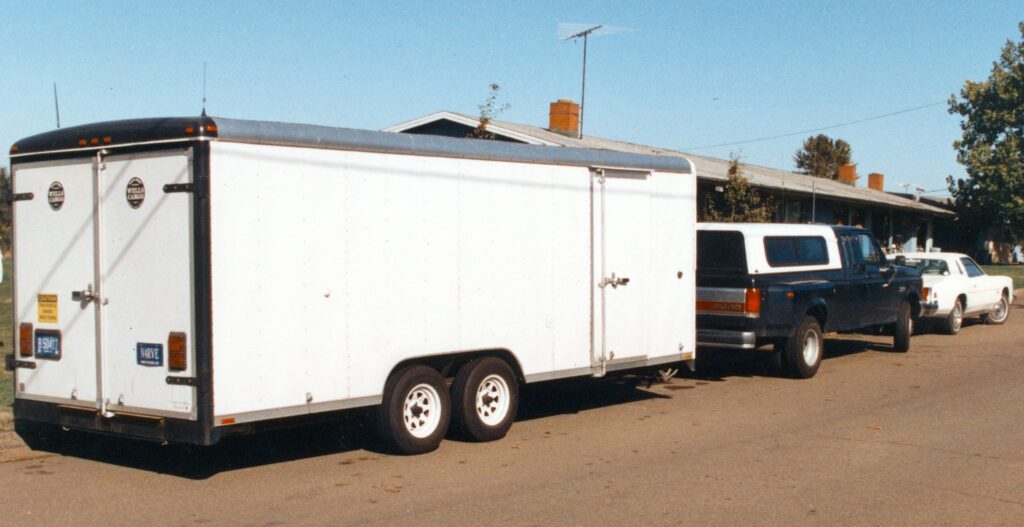
Launching the Microship Project
The 1992 decision to replace BEHEMOTH with a computerized solar/sail multihull launched me into a massive development project which has consumed more than 7 years of my life… and changed form so completely since the early days that some of these initial postings alternate between being amusing and embarrassing. In the interest of documenting the whole process, we are including the full series of posted documents on the development of the Microship. This begins in July 1993, and includes the full set of online postings and status reports published during that time.
This period can be loosely considered the birth of the Microship project — a time of struggling with newly recognized design trade-offs, refining the objectives, establishing sponsor relationships, and defining the control systems. This is the beginning of an incredibly complex project.
So join us now as we arrive in San Diego via the mothership (photo above) after a long quest for lab space, excited at the prospect of building a massively technoid sailboat in this sun-drenched beach town…
The Microship Project Finds a Home!
Steven K. Roberts
July 15, 1993
Yikes. I’m actually looking at two years in one place and feeling happy about it! Of course, as places go, this ain’t too bad: a funky summer sublet in La Jolla, my office in the UCSD engineering building, my lab in the old campus bookstore, my fabrication shop at Scripps Institution of Oceanography…. as well as Black’s Beach, the Mission Bay Aquatic Center, and a suite of essential life-support resources… all within easy mountain bike or bus range. Life is OK…
I’ve moved in here since my last report, and spend my days in a now-familiar pattern: flicker reluctantly to life, pedal to the office after filling my precycle mug at any of three espresso spigots, and disappear for hours into design details, email, and phone work until exhaustion signals midnight… then enjoy a quick flute jam in the acoustic wonder of cavernous concrete before pedaling home atop a shivering Vista-Light to collapse on the old bikelab futon. Some days offer respite: textile-free bodysurfing or bodywatching at Black’s, flying a windsurfer or Hobie cat across Mission Bay, or sweating my way along miles of tortured single-track aboard the very antithesis of BEHEMOTH while seeking out killer hills for pleasure. But there seems at last to have developed a balance between the seductive nature of this place and the equally seductive dream of aquatic nomadness (which takes work).
I’ll assume you’re aware of the basic objective of the Microship — a computerized trimaran that transports the whole BEHEMOTH concept onto water. With that as a starting point, let me bring you up to date, in a manner reminiscent of the “Notes from the Bikelab” series that started in 1990 as a weekly project status report. The past half-dozen or so issues have tended more toward adventure than the underlying nomadic technology… but then, the whole point of all this is that the two are inextricably intertwined, with no boundaries between work and play, passion and pinouts, methyl ethyl ketone peroxide and wanderlust. So now that I’m back to building strange new machines instead of riding one around (or, um, hauling one around on the show ‘n tell circuit), I hope you don’t mind the intermingling of romantic rhapsody with desiccant regeneration procedures, fiberglass Ku-band attenuation, and polyurethane foam deflection as a function of density and composite layup thickness. Hell, this stuff is FUN. Trust me…
I’m slowly accumulating volunteers among the student population here, and in a way this will be almost the opposite of the BEHEMOTH project. There, I had industry volunteers, people with deep experience but little time. Here, I’ll incur the added cost of some teaching time and coaching, but from what I’ve seen, the intelligence and focus of a student group can be formidable.
A lot of the work of the past month has gone into mechanical design — this is one of those wondrously complex projects in which electronic component choice affects gross morphology, which in turn defines constraints that affect the choice of electronics. Such psychological race conditions can only be resolved by tweaking the granularity knob until the correct solution congeals in a flash. Put another way, I form a fantasy of the desired results and allow input variables to float until an unanticipated combination satisfies the fantasy-comparator, pretriggering a snapshot of the conditions that yielded it before accumulated pondering-propagation delays introduced conceptual drift. (This is not the design methodology you read about in engineering textbooks, even though it’s a good summary of life in industry. Most textbooks promulgate the myth that structured methods and sequential procedures will get you there. But beating trade-offs requires inventing new rules to break, not bumping into the limits imposed by old ones.)
Ahem. There I go again. What I was trying to say is that the past few weeks have been a mind-stretching jumble of hatch placement, antenna coexistence formulas, weight distribution, human convenience issues, visibility, solar temp rise, salt-water exposure, modularity, fiberglass characteristics, single-point failure potential, hull-breach survivability, biological RF exposure, critical system redundancy, cabling issues, manufacturability, serviceability, CE/CLR relationship, and human factors engineering. Such things affect desalinator capacity, radar duty cycle, future upgrade paths, sleeping comfort, thruster power, dependence on shore resources, spares inventory, visceral bliss, network expandability, and just about everything else on board including where and how I go to the bathroom.
(This is the kind of stuff that is going to have to be parsed into finite projects for student teams by the end of the year… )
And so, after all that, there are some changes to the structure as postulated earlier. The hulls are still a trio of sea kayaks (a 21′ double in the center and two singles of indeterminate length), linked by a very critical structure of box-section stainless steel that can parallelogram sternward to allow transition into narrow-beam mode. Atop these beam assemblies are 4×10-foot solar arrays, hinged along their centerlines like bi-fold closet doors. 24 Solarex 30-watt modules (720W total) are laminated onto foam-core composite substrates, built much like rectangular surfboards. 35% of the way back from the bow is the mast step, supporting a sloop rig (a jib is a Good Thing on a multihull; else it’s VERY hard to complete a tack).
Hatch placement is quite interesting, and involves some of the hardest trade-offs of all. The outer hulls carry more or less standard kayak deck plans, with gear hatches repositioned to avoid interfering with the beam assemblies (AKA akas). The pilot’s cockpit (my home) is aft of center in the main hull, with my back close to the after aka (those are about 8′ apart, with the solar panels cantilevered about a foot at each end). A Linear recumbent bicycle, now enroute from flood-ravaged Iowa, may become the operating position, supporting as it does all the hardware associated with sitting and pedaling. The console is an uninterrupted Lexan sheet covering the 4 main screens and lesser displays, shaded by a cowling and mounted atop an already elevated coaming to allow pedaling clearance. Steering is a pair of sliding armrests with split-QWERTY keyboards (I haven’t ruled out the recumbent’s under-seat steering with chord keyboard, but it doesn’t FEEL right).
Directly behind the cockpit is a main gear hatch, bulkheaded to contain swamping. Ahead of it, likewise bulkheaded, is the head. As this machine veers further away from “kayak,” it encounters more and more the legal and practical issues that affect yachts — including lighting, anchorage, and sewage discharge….
All three areas named so far fit conveniently within the envelope defined by the solar panels — for this is also the tented area in bivouac mode. If I’m on water at night, I’ll cover this entire surface with a 10×11-foot freestanding tent, unzipping the floor to expose essential hull resources. (In blazing sun and harsh weather while underway, I’ll cover myself with a “bimini” that folds like a convertible soft top.)
Forward of the head, there is a bulkhead and main beam mounting platform that also includes the mast step. Forward of this is the main pressurized electronics bay, Qualcomm satellite antenna, a small gear hatch, and some glassed-in flotation foam. Aft of the after beam assembly is the tower for a small Furuno radar antenna, then a bulkheaded hatch for desalinator, water filtration and analysis, and the air compressor/tank/filter/dryer. Distributed all over the deck are antennas, radomes, grablines, cleats, and the myriad fixtures of safety and convenience. Even here, we encounter fascinating constraints — like the spacing between any two whip antennas being a minimum of three times a quarter-wavelength of the higher frequency. (And I thought the BIKE presented interesting problems!)
I’ll leave it at that for the moment… many other components are shaping up, but I learned from BEHEMOTH that premature publication of description is a prescription for contrition upon retrospection…
Project Updates from July, 1993
Most of this is derived from material transmitted via email to the Microship project participants and selected sponsors. It is important to remember that this is a real-time reflection of work in progress, and as this series proceeds, many statements made herein are guaranteed to be rendered obsolete. The good news is that this contains a wealth of developmental data, vendor information, brainstorming sessions, and trade-off analysis that is often lost in retrospective documents. But please do not consider anything in this series to be a final specification until it has been so stated.
As we begin, I’m proceeding on the assumption that the Microship will consist of three sea kayaks configured as a trimaran…
July 9, 1993
Spoke today with Joe Sedivec of Seda Kayaks, who is a Czech émigré and claims to be the first US sea kayak builder. He’s in National City, south of San Diego, and we have a meeting 10:00 Monday (just before he leaves for the LL Bean kayak symposium in Maine). I can’t tell yet if he’ll be interested in sponsorship, but he does seem very interested in ideas and publicity, and has worked with universities. He’s also local, has a good fab shop, and can deliver hulls alone or other subassemblies… so this should be worthwhile. I’ll take him literature. Need to speak with some kayak people and get a feel for his reputation for quality and seaworthiness, etc.
Also exchanging email with Dave Wright re solar wing assemblies. He agrees that glass over Airex is best, and suggests using diode isolation from each panel into charge bus to solve shading and damage problems.
I’m thinking about self-steering rigs, and the trade-off between a vane design such as the Miranda shown in Roth’s After 50,000 Miles versus electronic/servo. Electronics can fail at sea; the vane is simple but bulky.
In the training dept., I’ve elected to do Lasers on a 1-1 basis with Gary Reichel, and do the minimum necessary at Mission Bay Aquatic Center to allow boat rental. Holder (advanced) class probably will be cancelled, since it’s mid-week. I’m scheduled for Windsurfing this weekend, and Hobie starting 7/24.
I’m planning to begin setup of my electronics shop (old bookstore) this weekend, if we can pull ourselves away from sailing and Black’s Beach. It may become my home base on campus — easier to secure, funkier, and all mine as long as I need it. It’s also small and rather inconvenient to the engineering building. Will need to get the existing phone line extended there as well.
Also, although I’m certain about kayak amas, before nailing down a center hull spec I’m trying to figure out whether something other than kayak shape might be better. Perhaps a V-hull to reduce the need for a leeboard? More space? A place to go below? A few staterooms and work areas Oh, sorry, got thinking about F/27 and F/31 again…..
July 14, 1993
Had a great, though brief, meeting with Joe Sedivec of Seda Kayaks Monday (he’s off this week to Sea Kayak Symposium in Maine). I don’t believe he will be willing to sponsor boats per se, but may provide them at a token cost especially if I get a manufacturer to donate the glass/kevlar/etc. The Tango double (Cap 500 lbs, LOA 21′, Beam 29″, Depth 14″, Weight 95lb fiberglass or 76 lb kevlar) and Viking singles (Cap 350 lbs, LOA 16’6″, Beam 25″, Depth 13″, Weight 52 lbs fg or 38 lbs kevlar) seem like good choices, with possible alternative faster but narrower singles in the form of the Glider (Cap 375 lbs, LOA 19′, Beam 22″, Depth 12″, Weight 66/45). The Glider is more a racer, and provides less platform for the folded solar panels… also, my kayak cruising will probably be more of the placid touring style in which stability is preferred to zip.
Anyway, he’s in National City, and we’ll get together next week after he returns from Maine. He has project package #12, plus some media copies. His reaction to the package suggests that all sponsor packages should be assembled like this, with plastic covers and custom cover sheet including contents list.
Good telcon Monday with Bill Rever at Solarex. He agrees that the best approach is custom-fabricated panels without the .090″ aluminum substrate, cutting system weight drastically (aluminum has the same density as granite, y’know — and with standard panels the 80 square foot array would have .6 cubic foot of completely superfluous aluminum which would weigh exactly 99 pounds).
Anyway, since we don’t need the normal packaging, this also eliminates the border area used for mounting holes and grommets, and it may thus be possible to cram in a few more cells. The big issues now, from the Solarex perspective, are cell layout, spares inventory, serviceable lamination technique to the foam-core, thickness of Tedlar sandwich, and electrical termination. The latter is especially critical, since we need to get wires out of a very flat object without allowing aqua regia (seawater) to wick in. He proposes some kind of a bus rail or channel along each outer long edge to protect the terminations (and house the diodes and sense lines), though I’m very wary of anything that can trap water. This will be an extremely harsh environment, exposed to sunlight, saltwater, flailing feet, thermal stress, flying fish, folding mode changes, and rough handling when disconnected from the boat. I’m tempted to recess the substrate mold and run all this stuff down — or perhaps capture it in a raised wall that doubles as one boundary of the rainwater catchment surface and triples as a grabrail for safety.
In the education dept., I’ve just finished After 50,000 Miles by Hal Roth, an excellent commentary on the issues of full-time cruising (dated 1976 and not totally relevant to the Microship, of course, but useful). I’m now into The Fiberglass Boat Handbook by Jack Wiley which is providing lots of insight into materials, layup techniques, and structures.
Attempted call to my GPS sponsor at Motorola, who is out until 7/26. I wanted to swap Traxar for new model, get the Core unit to aid in deck layout planning, and revive the contact with Radius division which may sponsor Marine VHF and GMRS handhelds. (RE the deck planning issue, one of the things we MUST do soon is get all deck-mounted devices in-house, since this will impact packaging.)
Telcon today with Steve Salman, referred to me by Jean Polly for info on ham radio data links to internet (told him re AMTOR/APLINK). He’s preparing to cruise around the world in a 40-foot yacht, and will be here in October. We talked of nav aids and such, and he’s a strong believer in my having a small marine radar unit, even if mounted low (though I’d probably want to erect an absorptive barrier so I can hide my body behind a blind spot to prevent biological damage…). This could be a packaging nightmare, but is worth exploring. Contacting Furuno tomorrow re their 1621 LCD micro-radar, which has an 8.8 pound radome and a 6″ diagonal LCD in a 2.6″ deep case.
Req’d data from Astro Flight on efficient DC motors (Venice, CA) for the thrusters. My earlier assumption that we would use variable reluctance might not be too sensible — they are overkill with their ability to act as brakes, steppers, generators, variable-torque motors, etc.
Another thought re beam assemblies: efficient sailing may suggest the need to have the windward float (outrigger) flying. It might be possible to add a mode whereby they can be cranked up a few degrees instead of always lying parallel to the waterline plane…
July 15, 1993
Last night worked on sponsor database… still fretting over suitable platform. ACT! is feature-rich but annoyingly cumbersome at times, with at least one nasty bug and extreme resistance to convenient importing. Yet it does interface smoothly with GeoQuery, which is why I have it. TouchBase, which I’ve been using, is brisk and efficient, but doesn’t support Apple Events or provide the contact management features. The problem is keeping track of myriad relationships with ~500 companies and individuals associated with the Microship project, as well as my much larger PEOPLE database of nearly 5,000 contacts which must eventually be geocoded for integration with the boat’s mapping and navigation system.
Just received a box of sample rigid polyurethane foam blocks from General Plastics in Tacoma, to whom I was referred by Clark Foam which no longer sells stock slab. The product line is called “Last-a-Foam” and includes material with densities from 3 to 40 pounds per cubic foot. This is the core material for the solar panel substrates. I have detailed spec sheets and samples of 6 densities here for anyone who wants to take a look… the plan is to follow up on last week’s contact with Skip Frye Surfboards to find a fiberglass shop willing to vacuum-bag layup the panels once we have precise dimensions and attachment point specs. (This is so much like surfboard design that it would be foolish to reinvent the wheel…) I’m thinking of four 2×10′ panels, although the foam only comes in standard sizes up to 4×8′. Theoretically, it’s not really critical structurally, so given a suitable joint, using two pieces shouldn’t matter.
Telcon with Kevin at Marine Electronics in Hartfield, VA. They are US dealers of the Furuno 1621 LCD Micro-radar, and specs are enroute. He also feels that full or partial sponsorship is likely (the retail price is a surprisingly low $1350). Antenna height is not critical since we care about things within nav range anyway (each additional 10′ only buys about a half a mile), though I would want it either above my head or hobbled with a blind spot by an absorber so I’m not getting irradiated (though it might warm me on cold days….). Power in transmit is 30W (12V). Physical packaging would permit excision and console mounting of the 6″ diagonal LCD, with the user interface emulated by control system software.
Perhaps this radome and the Qualcomm one could be integrated into a single column, since this looks at the horizon and Qualcomm looks at the 20-60 degree elevation range.
Must go sailing. Life’s a reach, then you jibe….
July 16, 1993
TJ Tyler comments on my notes about foam-core in yesterday’s report:
“Well, I am curious about only being able to get 4×8″ sizes. Especially considering you were talking with the people at Skip Frye Surfboards. Skip specializes in long-boards, and many of those boards are over 8′. If you talk with the right people, you should be able to find nice, 10′ lengths. Also, since when did Clark Foam stop selling blanks? We got some stuff from them not long ago for our HPV fairing. I find that equally odd.”
Also, Dave Wright in Santa Cruz responds to an earlier letter requesting his comments on vane versus computer-controlled steering:
“Vane steering is the way to go as far as reliability is concerned, but I think you are confusing big boat needs with what you are building, which is a daysailer, despite your imaginings to the contrary. If you want to overnight then get something that has a cabin, otherwise forget it. Don’t build BEHEMOTH rev 3.”
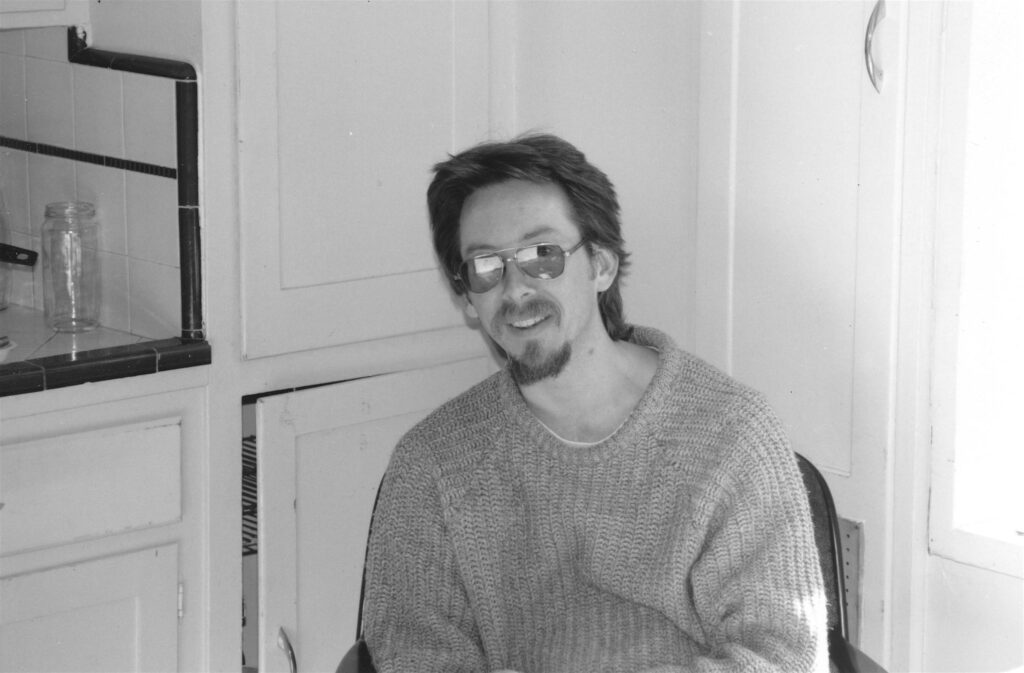
I’m not so much interested in remaining under sail overnight, but in having something singleminded and tireless take the helm for a while to let me relax, work, video, etc. I’m not at all interested in ocean crossings, though there may be some long reaches now and again. It’ll be a while before I’m confident enough to go to sleep while the boat is in motion, at least if I’m alone on it!
BTW, re the overnight issue: I firmly believe that it is necessary to sleep on the water sometimes — most likely when there’s simply no friendly place to beach it and camp. I’ve learned this from kayaking… the best areas are developing pitched battles between hordes of waterborne explorers and fiercely territorial coastal landowners who write nasty letters to magazines when someone slips onto the beach to take a break. My on-water bivouac mode involves tents on solar panels.
In other news…
Long, sweaty day. Thanks to the help of TJ Tyler (Mechanical Engineering) and Mark Overbaugh (an 11th-grade volunteer) — then later a whole horde of TJ’s friends — the electronics lab in the old bookstore now contains everything that was in the mothership and much of what has been stored at Scripps “Seaweed Canyon” (which will be used for fiberglass and large fabrication work). Disassembling the mobile lab was rather painful, but this will be much more useful. The new lab is not at all set up yet, but the components and major furniture are now in one room… having technical workspace will help a LOT. First steps, irrelevant to this mailing list but important to me: security, phone, and decent lighting. I’ll comment occasionally on this overhead, but not bore you with details.
July 17, 1993
I’ve spent the whole day building databases. After agonizing over the ACT!-vs-TouchBase issue for a few weeks, I talked with my manager (Barbara Chase) today and she suggested FileMaker Pro. After she stepped me through it on the phone it started to look rather appealing, so I spent the afternoon and evening building the structure of the new Contacts and Products databases.
This sounds like boring business stuff, but this is the core data structure that will provide geocoded human contacts to the Microship’s mapping system, as well as put all my 4,500+ contacts at last into one place (including sponsors). And this central repository of people is now linked via a simple script to the database of system components, so we can look at the record for the life jacket, for example, see its weight, value, spares inventory, notes, and other specifics… and also display a link from the relevant sponsor record (Extrasport) for contact information. Hopping over there for more details, we see all the details of the business relationship, as well as flags for hospitality invitation and a dozen or so other interesting specifics. This solves the problem of multiple records for one company name confusing things, and eliminates my traditional pair of overlapping databases for people and sponsors with the attendant loss of synchronization when addresses and contacts inevitably change over time.
Now all we gotta do is import the data …
FileMaker Pro is quite elegant, by the way… amazingly flexible in all respects at the creation end. I have yet to see how briskly it handles large files, but I’ll be pleased to get rid of ACT!, which has proven itself clumsy and confusing, heavily feature-laden for contact management yet lacking some real basic database essentials.
July 19, 1993
Coffee conversation with TJ today has rekindled the nomadic community idea — over the years I’ve had quite a bit of interest from people who want to travel as a sort of high-tech nomadic tribe. I’m thinking of a little standard waterproof box that can fit any kayak, pedal-craft, or small sailboat — providing connectivity to a wireless network linking all the boats and delivering status data, basic navigation, security, email to and from the Microship satellite Net gateway, etc. That plus marine VHF and a simple solar power system should allow anyone to plug in to our nomadic aquatic community without a major packaging and development project. Now here’s an extra motivation for working on this system… for those with a yen for adventure, the 2-year development effort could pay off with adventure! A few years ago I published a Call to Nomadness that described how this could work with a number of bicycles, and had 80-100 responses from people who wanted to explore it. Unfortunately, it was just too much for one person to manage, and thus never happened… but here in the University environment, it may be more realistic since there will be other people involved from the start.
I made the formal proposal to Autodesk for a copy of AutoCAD Release 12 for Macintosh… they told me a few months ago that it would be easiest if I could give them a University address. I dragged my feet, trying to decide whether to go with Mac or DOS, but TJ pointed out that DOS versions are readily available around campus if I need them so I might as well use what feels good.
In the interest of nailing down enough of the mechanicals to begin some serious design work, I’m trying to identify all console and deck components that will in any way affect the fiberglass work. Here’s a preliminary list… the first is limited to console devices, which will be mounted on a flat panel screwed into a gasketed, pressurized nacelle. The second list includes items that are actually on the deck itself.
Console devices
- Marine VHF control cluster
- Displays:
- Macintosh LCD (active matrix, maybe color)
- Color video monitor LCD
- Control system LCD (probably low-power DOS for simplicity)
- Radar LCD
- Digital Panel Meter, cycling though key measurements
- Clock
- Switches:
- Running and anchor lights
- Chart/console light
- Bilge pumps for each hull
- Guarded EPIRB
- Control system power
- Wake-Mac pushbutton
- “JATO Mode” — all power to thrusters
(BTW, it may be worthwhile to consider “reflective” LCD packaging inside deep nacelle to minimize solar temp rise and lower the overall cockpit coaming profile. Also, some components may be mounted INSIDE the cockpit for tamper-resistance or clutter-minimization. A further thought: all LCDs mount behind a single smooth Lexan panel with no openings, with a different sub-panel for the few controls. Easy to change as computers and display technology evolve… no waterproofing or thermal cycling headaches… simple… pretty.)
Deck fixtures and major mechanicals (center hull only)
- Qualcomm satellite radome (abt 12″ dia), poss under glass
- Radar antenna on raised pole (enough to clear my head)
- (mizzen and self-steering mast with antenna on top?)
- HF Vertical antenna (sloper to mast?)
- 2m/70cm/marine/RF-LAN/scanner/differential/cellular whips
- EPIRB
- GPS
- Microwave motion radome (poss inside fiberglass)
- Radar detector/DF antenna
- Console assembly for each cockpit
- Keyboard, rudder controls, etc.
- Deck compass (backup – electronics fail!)
- Running lights (including bi/tricolor on mast)
- Speakers
- Water server spigot, intake, and manual pump (prob in cockpit)
- Environmental sensors as needed (minimal deck impact)
- Manual bilge pump
- Compressor intake (bay pressurization)
- Diving compressor I/O ports
- Boom microphone on console cowling
- Main Electronics bay (lift-out pressurized box on umbilicus)
- Gear stowage hatches (2)
- Tent mounting fixtures
- Video head/turret
- Cleats, U-bolt for security, grablines, etc.
- Receivers for folding beam assemblies (amas)
- Crane-lift eyebolts (4 – probably about 1′ out on beams)
Most lightweight gear, clothing, food stores, and the like will be stored in the standard hatches of the outer hulls. Center hull will be busy with systems, flotation compartments, human space, pedals, easy access gear, emergency supplies, water processing, etc.
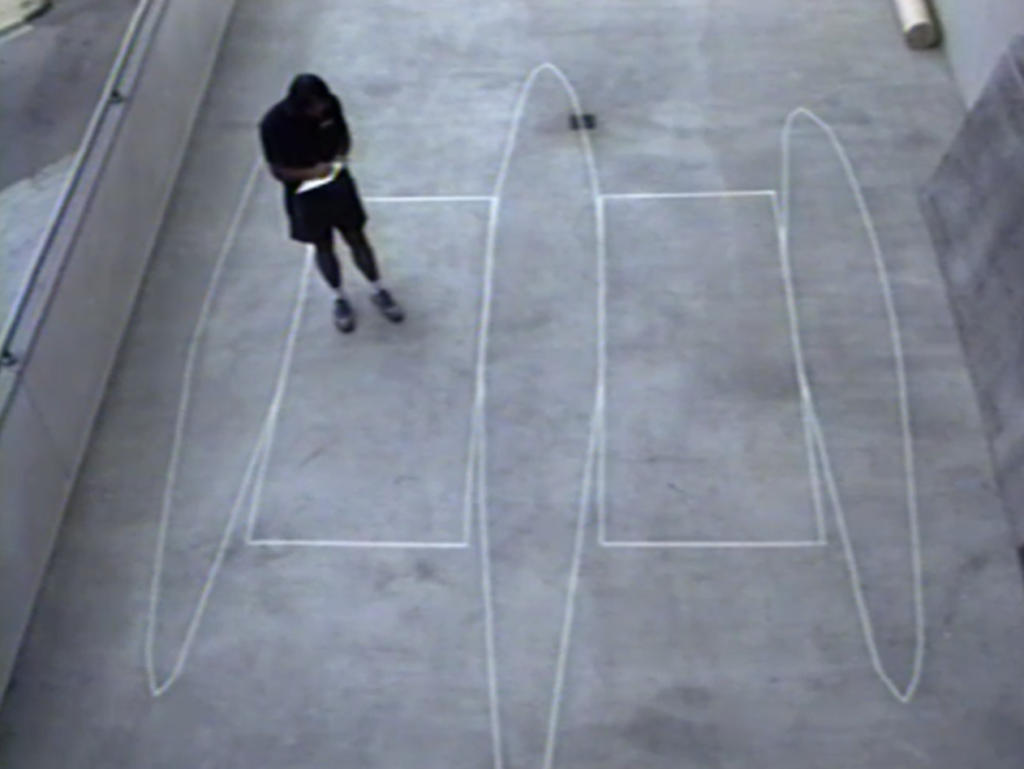
Early this evening, TJ and I built a full-size “drawing” of the Microship with masking tape on the patio outside my office. Very instructive… being able to walk around it and FEEL the dimensions goes a long way toward developing the overall layout.
Issues now are placement of hatches, mast, and beam attachments. Do we need a large electronics bay, or a small one? If it is to support two people full-time, how do the cockpits coexist? Should it be designed for one, but accommodate a passenger without major support facilities (a rumble seat)? What happens in the cracks between solar panels and inward-curving hulls? Having a full-size layout greatly facilitates decisions like these.
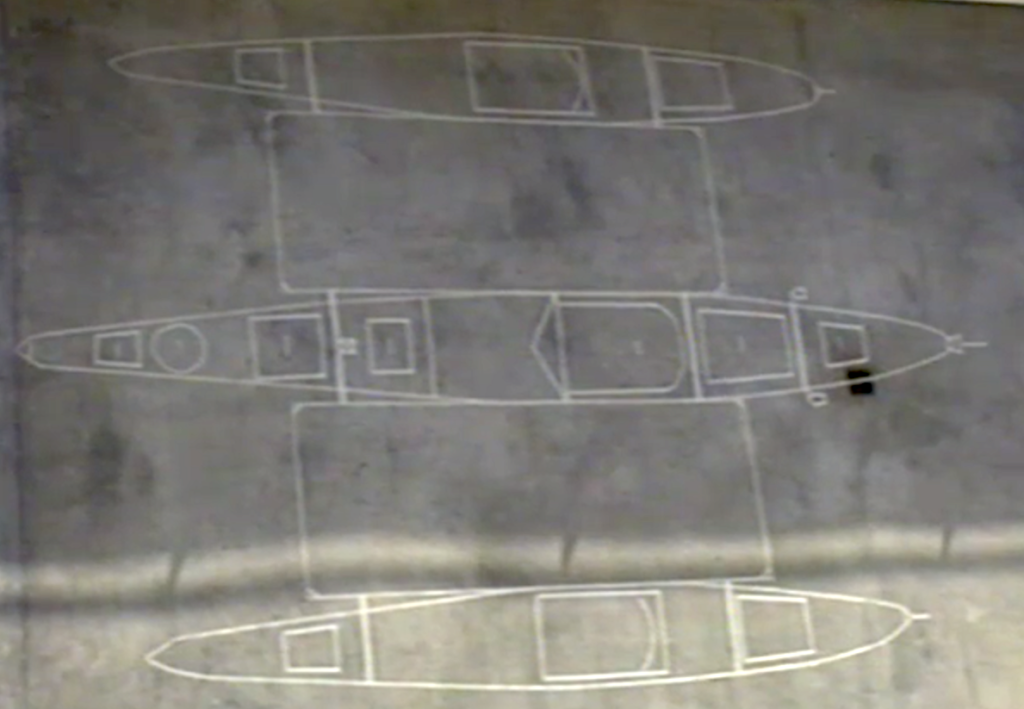
July 21, 1993
Spoke with Karen Parks of General Ecology re water filtration, and she suggests their Base Camp model in series with a bypassable reverse-osmosis desalinator. The Base Camp is 60 oz., handles 2-4 pints per minute, and required filter service or replacement at about 1,000 gallons. We’re sending a proposal. (The thought of a reliable water processing system on board is very alluring, especially after reading the news about Mississippi River flood victims in the midwest!)
I also spoke with Dave at Village Marine Tec re their reverse-osmosis desalinator. The catch with these is that they require about 800 PSI for seawater conversion, which means heavy hardware. Eliminating all cabinetry and overhead, they can get their “Little Wonder” unit down to about 30 pounds. . Anyone know of a lighter way to do this that still lends itself to system integration?
Autodesk responded with a solid YES to the AutoCAD proposal, and Release 12 for the Macintosh, as well as AutoSurf surface modeling software for DOS, is on the way. Refined the full-size CAD (Concrete-Aided Design) layout on the patio… preliminary arrangement of hatches and major deck fixtures now established.
July 23, 1993
Sponsor news: Spoke with Steve Hansel of Linear Recumbents in Iowa (along the river, but enough uphill that he’s not flooded, in case you were wondering), and he is shipping a bike for the project. Reason: I’m thinking that the cockpit should consist of receivers glassed into the hull and a drop-in recumbent bicycle for seating and pedaling. In land mode, I’ll just pop out the bike, attach wheels (stowed somewhere!) and pedal away. Dave Berkstresser suggests having the aluminum parts, including this bike frame, treated with the “Tufram” or “Everslide” processes, which involve hard anodizing with a Teflon seal suitable for salt water.
July 26, 1993
I’m having discussions with the campus police about security — they describe the bookstore building as a “sieve.” Clearly, I’m going to have to spend some money on locks and additional security systems, including a remote monitoring system that lights a status indicator in the police dept. It all feels pretty scattered now, with my operation spread over three mutually distant sites… I’m hoping to expand soon into a single space that can hold everything. This will become particularly messy when boats are on hand and we’re trying to build molds, do drawings, fit components, and plan layouts… I wonder if it will all get shoehorned into the lab to minimize running-around time?
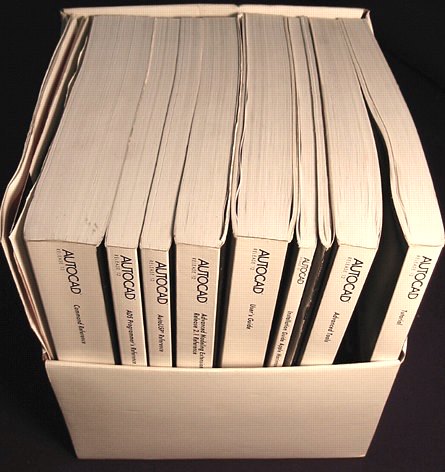
AutoCAD Release 12 for Macintosh arrived today, and it wants System 7.1, external monitor, and at least 30 MB of free disk space. Might have to dedicate my dormant SE/30 to this… I need to find someone who wants to do the configuration and installation. I think this would overload the PowerBook, which is my management and communication machine.
Bob Heil of Heil Sound (microphone guru) suggests one of their elements in a small stub/boom, waterproofed with mylar, mounted directly on the console and aiming at my face. I contacted him to inquire about alternatives to head-mounted and hand mics, both of which would probably get trashed in the marine environment. Sending lit.
Had private lessons yesterday on Hobie 16 catamaran… off sometime this week for a reality check in the form of sailing one in the ocean. I’ll be paying particular attention to effects of high sail aspect ratio, multihull behavior in swells, general cross-member stresses, fore-aft hull trim and its effects, and what happens at the edge of panic if we start to lose it. None of this will be quite the same as the Microship, but the Hobie is the closest thing readily available for initial hands-on training in real conditions.
On the hull-design front, I spoke today with Joe Sedivec of Seda Kayaks, and he basically agrees to do the boats if I get about twice the required materials donated (or pay for labor and get the required materials donated). Small company… sponsorship not likely. In other words, he’s willing to sell me boats, albeit in a non-traditional fashion. He provided a list of major fiberglass/kevlar vendors:
- DuPont Kevlar
- Clark Schwebel
- Burlington
- JP Stephens
- Hexcel
- Owens-Corning
We need about 200 pounds of raw material total for the three boats.
I also spoke with Matthew at Current Designs in Sidney, BC (Brian Henry, pres., is kayaking in Greenland), and got some dimensional info on their present kayaks as well as large-capacity “Libra” double under development. In general, I’d prefer to work with a high-visibility, high-quality vendor like this, though Seda is local and has been around a while, keeping costs down with manufacturing in Tijuana. Local vendor could be useful when it comes to all the weird deck issues on the center hull…
I’m trying hard to nail the overall mechanical design so it becomes possible to spec hardware… this evening has mostly been spent in consideration of major component placement. One problem that I’ve overlooked until now is waste management… there are “No Discharge” areas all over the prime boating areas, and enforced legal requirements for holding tanks. (At some point, this is going to stop looking like a kayak, and will no longer fall through the legal cracks affecting running lights, sanitation, berthing, licensing, and so on.) The traditional kayaker’s approach of an ammo box and some plastic bags is not particularly appealing for extended travel, nor can I assume easy beaching whenever necessary. I believe the answer, as insane as this may sound, is a small marine head (about 20 pounds for the littlest one in the West Marine catalog) located in the hatch just aft of the mast. A small bimini (or the main tent) covers this area, and without getting too detailed, it appears that the geometry is about right. This leaves the main gear hatch behind the cockpit available for packs (as well as both outer hulls, of course).
July 27, 1993
Telcon with David Phemister, resident wizard at Larsen Antennas. He’ll provide whatever whips needed; I’m sending him a list. Although they don’t have a marine product line per se, their stuff is vastly better in RF performance than the common marine antennas. Dave advises glassing in ground plane (copper mesh OK, same as I’m using in hull for capacitive coupling to seawater) as well as provision for physical connection to it at antenna mounts.
Rule of thumb for inter-antenna separation: a minimum first odd multiple of a quarter wave at the highest operating frequency. Example: UHF and VHF separation should be at least 3 times the approximate 6″ wavelength of UHF; cellular works out to about 10.5″ from its nearest neighbor. Violating this results in bad matching, shadows, reflection, and other nasties.
FYI, they now have a 14db 7-element cellular yagi to replace the 10db 6-element unit I used for a while on the bike. This is relevant to offshore cellular use, extending effective range of a 3-watt phone to well over 100 miles (I tested the other one to about 130 miles under perfect conditions).
Telcon with my GPS sponsor at Motorola (Automotive Division, Schaumburg, IL): he’s sending the new CORE GPS receiver for boat installation as well as the upgraded Traxar to replace my handheld. They will both interface with a differential receiver, yet to be marketed, but he’ll send specs on packaging and antenna mounting so there won’t be any surprises (the receiver is a very low freq., like 256 kHz). Issues on the CORE include cable length (15′ coming for tests, but probably too long… very hard to splice since it’s an active antenna), and antenna mounting (they don’t have the low flush-mount like Trimble does, but are optimized for relatively fragile marine pole mount, which I don’t really want).
Also, I’ve been referred to the right contacts in Motorola for handheld GMRS transceivers for utility use and the Triton series of Marine VHF. These are notably bigger and heavier than Icom’s, but have some of the best specs in the industry. We’ll look into remote panel operation.
Telcon with Donna of Skip Frye Surfboards led to contact with Jay Livesay, boatbuilder. He may become involved in the fabrication of the foam-core panels, but says I should contact Corsiar Marine (maker of the F/27 trimaran) if I want the ultimate in local high-tech composites wizardry.
July 28, 1993
I had a very good meeting with Yvonne Andres, of the NSF-sponsored Global Schoolhouse Project. We’re identifying a number of ways the Microship adventure can be integrated into K-12 curricula (environmental monitoring, video conferencing, interdisciplinary project development, sociological and cultural issues, nomadic connectivity, internetworking, lifelong learning, etc.), and will see if there’s a way to make it happen without severely impacting my time. If all goes well, this could translate into some funding… altruism is a fine thing, but time and money are scarce (and interrelated) resources. I’ll keep you posted.
Qualcomm is receptive to the new satellite station proposal, and we’re now working on details… more as it develops. I’ll probably get mechanical samples in the near term for packaging design, using the existing bike installation for network tests… then swap when the Microship starts to go live.
Did some research this evening into air filtration and drying for the equipment bay pressurization system — looks easier than I thought. The massive McMaster-Carr catalog lists at least one small desiccant filter that can be regenerated by heating to 350 degrees (that’s what the Outback Oven and Peak 1 stove are for, right?). Looks like the system will consist of an inlet filter, compressor, water/particle filter, air tank, gauge, and regulator down to the 3-4 psi we’ll want for the bays. This is fairly high-volume, and some P-V calculations will be required to properly scale the components. I’d like the tank to carry 100-150 psi for other applications, with regulators as needed. It must be sized to keep the pump from cycling endlessly on otherwise idyllic waters…
July 29, 1993
Another good apps engineering discussion with Solarex today. One of the unfortunate effects of solar panel design is that they work optimally when cool, and must be derated in voltage output (about .4% or about .08V per degree-C) at elevated temperatures since they’re about 90% absorptive. Since the Microship array will be mounted on insulating foam-core, we can expect operation around 30C above ambient, or 12% derating. (In other words, for best performance, don’t put your solar panels in sunlight!)
There are other issues, though. First, these will be VERY HOT surfaces in full sun and still air, something I can confirm from BEHEMOTH trailer experience, and I’ll be sitting right between them. They could run as high as 80 deg C! During long static spells, I could cover them with white cloth, which would still allow battery trickle charge without the unpleasantness of the high temperature (which accelerates diffusion effects and other life-shortening phenomena as well). Also, we must be sure that the composite structure itself can withstand these temperatures, as well as the stresses of cycling.
Also, further discussion of termination suggests avoiding the rubber contact blocks as are used on the bike’s solar panels, and instead bringing leads out the back with an RTV seal. This dictates a shallow trough in the substrate, suitably glassed and foam-filled, that carries the power bus, isolation diodes, and sense circuitry.
You must be logged in to post a comment.