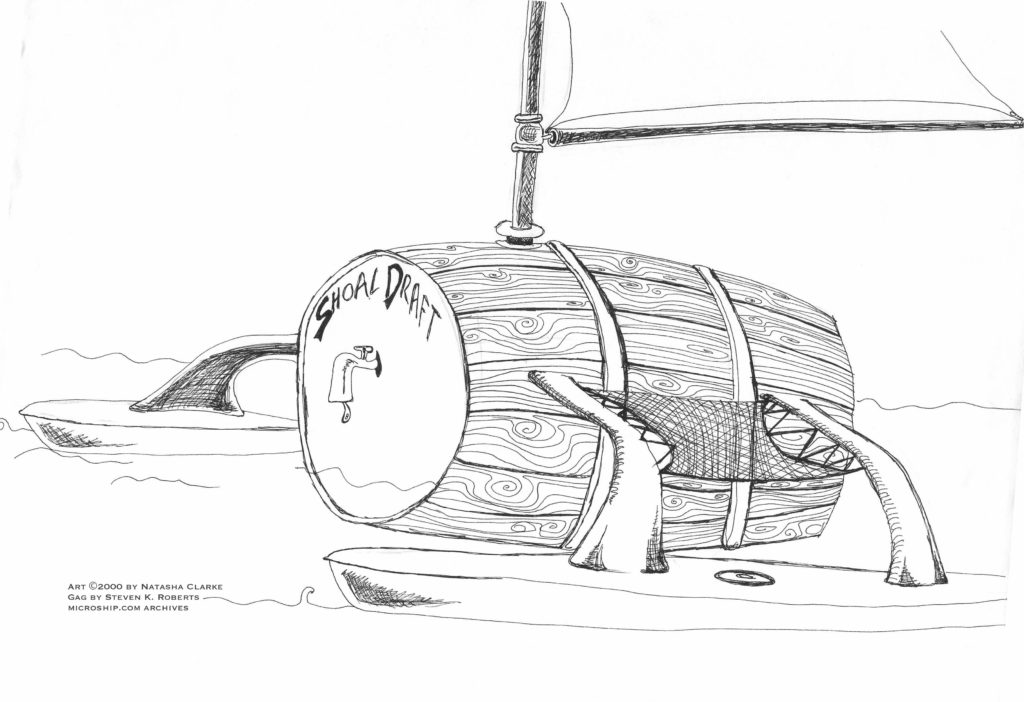
Cat vs Tri
OK, let’s lay it out analytically. Cat versus tri? Tri looks most sensible for lots of reasons, and we target the 30-foot range at $15K. Build versus buy? We don’t want to be boatbuilders. Hoping to conjure something with a clear enough spec, we lay out a full set of requirements…
The cartoon above, based on one of my old bits of wordplay, was done by Natasha Clarke about five years after this post was written.
Microship Status Report #84
by Steven K. Roberts
March 12, 1995
CAT vs TRI
You know, this process takes a LOT of patience. Those of you who are reading these reports as they are produced (rather than in print or archive form) must be tapping your feet, muttering something about getting on with it. After all, we have considered damn near everything (except a monohull) over the 2.7 years since this project was conceived, and while we have made tremendous progress on many fronts, that essential question — what boat? — remains stubbornly unanswered.
Well, we’re getting closer, and fast.
I’m treating the start of next quarter as a deadline for the final decision — by mid-April, I want to have, at the very least, a full set of drawings for the eventual Microship substrate. As such, we’ve been focusing on this issue heavily, talking with multihull designers, owners, and industry observers as well as defining our own specific needs. The bulk of this issue will be taken up with as complete an overall spec as we can produce at this time.
The interesting thing that is occurring is rapid convergence upon a very specific class of boats — demountable trimarans in the 30-foot range. Larger boats become increasingly expensive and hard to trailer; smaller boats are too small for two people to live aboard in the company of extensive electronics and technomadic support systems. Also, smaller boats suffer in the seaworthiness and load-carrying categories.
The 30′ catamaran I discussed in issue #83 seemed ideal for a while — we even found a builder in Oregon who is about to produce two of them, and would do our hulls as well as centerboards and rudders for about $6500 (2x materials cost). But continuing analysis of the options, including a long conversation with multihull architect John Marples, yielded the following observations on the cat vs tri issue:
- Small cats have hulls too narrow for comfort. While two hulls are appealing in principle to keep two people sane, they are, if trailerable, less than 4′ wide at their beamiest point. Take a piece of chalk and draw a 4′ wide hull form with less than standing headroom on the wall, extrude it in your imagination to 30′ with sharply tapered ends, then imagine living in it. Cats over 50′, or those with wingdeck cabins, are a different matter and are larger than tris of similar length… but those are too expensive and don’t meet our other needs.
- Small tris have much better communal space than small cats. It can be nice to eat, sleep, and work together on occasion.
- Cats have two centerboards, two rudders, two cockpits, two heads, two bow structures… two much redundancy! Of course, tris have THREE hulls, but the outer ones are passive and simple.
- Cats must be stronger (heavier) to make up for an intrinsically weaker structure. The main hull of a tri is a torque tube, with centralized torsion and better load distribution. Cat crossbeams are severely loaded by rigging stresses.
- Tris are less prone to underwing slamming, since the gaps between floats are narrower.
- Tris are MUCH easier to fold up and trailer, and, if so designed, lend themselves better to on-water compression schemes for narrow slips and ramps.
Without specifically naming a boat at the moment, I will say that we appear to be back to a trimaran — and are now evaluating a small number of options in the same general size and price range (30 feet and $15K).
BUILD vs BUY
Another major decision is best expressed, given our budget, as “do we buy a used boat and majorly hack it, or do we build something around our needs?” The latter would seem the obvious answer when expressed that way, but the industry abounds with sad tales of unfinished homebuilts — Bob Payne mentions in Sail this month that “the average completion time for a home-built boat is 130 years.”
While he’s joking, there is some truth in the statement, and I’m also wary of entering a project that entails large, non-amortizable fixture and tooling expenses… not to mention a whole new suite of learning curves. Still, it must be considered as an option if no suitable boat is available off the shelf, and there is the possibility of engaging the services of a well-equipped, experienced builder. I have no illusions about building being any cheaper — the goal is simply to find something that meets a complex and specific set of needs, not so easy with stock boats. Fortunately, some very simple wood-and-epoxy methods have been developed, so if it comes down to that, well…
In the meantime, let’s get specific. We’ve needed a solid set of specs for quite a while, so the rest of this issue is devoted to nailing down the real requirements of this boat.
MICROSHIP 3.0 INITIAL SPEC
Space Distribution
Faun and I need a good open living space with standing headroom, a commodious bed of 35 square feet (that’s a lot of bunk!), galley and head facilities, our own offices with integral Macs and closable doors, and a cockpit that allows full access to all computer and communication resources. By providing both fore and aft exits from the cockpit, we have separable areas — linked also by crawl-through tunnels that double as single berths for guests or the occasional need to escape each other.
Here’s a brief description of 10 living and stowage areas…
Cockpit
This is the Microship’s control center, and is a sort of well in the deck that can be covered in bad weather with a dodger, or, if we’re clever with packaging, a retractible hard top. All sail controls are present here, so there has to be room for line clutter, winches, and so on. This is also the steering station when we’re not under autopilot — given the need for protection from the elements, this is not a tiller but a cable-linked pair of control levers or some other control that provides tactile feedback. A folding tabletop provides a surface for charting, eating, and the like; two seats face forward or swivel inward, and the console forms a sort of dashboard in easy reach of the pilot (nominally seated on the right). This consists of 6 screens: Macintosh for graphic control and general computing, 486 for the charting and weather image system, color video, radar/nav, Hub low-level display, and power monitor. A DuraPoint waterproof pointing device is built into the armrest, and a removable waterproof keyboard can be fitted when needed — though it’s not required for normal piloting operation. Other than this, there are minimal user inputs — light switches, security keypad, VHF, and nav system controls — everything else runs under HyperTalk via the FORTH network.
Lab
Exiting the cockpit aft, down a small ladder, leads to my lab and office. This is also the “chart table” and general plotting area, as well as the repository of tools, diagnostic equipment, and so on. The walls carry power panels, other comm gear, pneumatic system monitors, engine displays, and other hardware that would clutter the cockpit. The space above my desktop folds open to expose a pressurized enclosure for the control systems, providing a convenient workplace for hardware hacking. This area also contains the video production tools, documentation library, and protected stowage for all sensitive equipment.
Berths
Sealed hatches allow direct passage from the lab forward, without passing up through the cockpit. The amount of hull flare and other dimensions will affect the quality of this space, but the objective is auxiliary stowage and sleeping space for guests, berth for an off-watch partner, or simply a place to be alone for a while. The interior walls may also simplify access to the space under the cockpit.
Battery/generator Compartment
Below the cockpit and between the berths are the heavy parts — 180 pounds of diesel generator (6kw) and about 250 pounds of batteries (also charged by solar and wind — see below). Access for service is via sealed panels in the lab and cabin, with cockpit floor removal possible to enable lift-out if necessary.
Cabin
A critically important area for long-term sanity is the cabin, accessed from the cockpit via a second companionway ladder a couple of feet in from the port side and in line with the walkway between galley and living area. The idea here is to have a large comfy bed that folds up to yield seating and table (a kick-up centerboard trunk has to be accommodated). The bed is oriented fore-aft and as far to starboard as possible; the galley equipment is all along the port wall. If our schedules are in synch, we’ll just mode-change the bed morning and night; if we’re alternating watches, the off-watch partner can crawl into one of the berths to allow the other easy galley and head access.
Head
A small room forward of the bed houses head, shower, and sink. We’ll have a watermaker aboard as well as rainwater catchment, and hope to find a small demand water heater for the luxury of a hot freshwater shower (with a hatch overhead to vent the moisture). The type of MSD (marine sanitation device) has not been chosen, but will include a holding tank and waste-processing system.
Closet
A small stowage area is forward of the galley, across from the head.
Faun’s World
At the bow is Faun’s desk, integrated with the forward bulkhead. Like Steve’s world at the stern, this area can be closed off for privacy, and includes a Macintosh sealed into the wall before the desk with fold-down waterproof keyboard and pointing device. There’s also another slave display from the Hub, since it continuously updates its LCDs with all status info, nav data, power conditions, alarms, and so on.
Sail Locker
Accessable via a hatch on deck is a sail locker in the bow, sealed from the rest of the ship (this is the area most likely to become holed in a collision). There may have to be some provision for anchor rode/chain herein, but we may prefer to use tubular nylon webbing on a reel topsides.
Amas
Finally, there is limited stowage in the amas for bulky, lightweight items like fenders, spare PFDs, dried food inventory, and so on…
General Ship Requirements
The Microship is intended for a wide range of conditions, and we’re planning on a number of enhancements that will shape the substrate in various ways. To help keep those in mind during the design process, here are the key objectives and special considerations:
Seaworthy
This probably goes without saying, but whatever our conservative coastal/river travel plans may be, it would be foolish to build something that would be destroyed in the first offshore gale. The ship must have adequate freeboard, good pointing ability, a seakindly ride, good reserve buoyancy, an inverted waterline conducive to survival after capsize, and very rugged construction that’s also easy to repair. Good sailing performance is important as well, but not on a racing scale — we’d rather err on the side of reliability.
Road Mode
In addition to operation on water, the boat MUST be trailerable. We’ve agonized at length over just what this means, and have always assumed an integral trailering system that can be deployed and allow hauling with a rented tow vehicle. Realistically, this involves too much heavy hardware for our weight budget, so the compromise might be small wheels that are adequate for haul-outs and short range portages. A flat-bottomed hull coupled with careful planning and crossbeam-folding could allow long-range highway transport via a rented flatbed truck.
Loading
The weight study and the boat design interact in a circular way, so it’s difficult to quote a number until we iteratively home in on a design to go with it. However, all recent estimates and spreadsheet calculations point to 1500-2000 pounds of gear in addition to primary structure, rigging, and crew. This figure is conservative, and includes batteries, engine, tankage, electronics, kayaks, stores, and effects.
Shoal Draft
This should automatically go with being a multihull, but just to reiterate — the boat must be beachable, with a robust enough keel to withstand point loads of rocks and the abrasion of bottoming. The rudder and centerboard must kick up non-destructively. It must be possible to beach the boat (or haul out on the aforementioned wheels) and camp securely on board.
Narrow-beam Mode
It must be possible to retract the amas to two distinct levels of compression: on-water beam reduction to 12′ or less for narrow slips, and off-water folding or demounting to fit the requirements of highway transport (8.5′, though 8′ is a better target).
Kayaks
The boat will carry two Current Designs rotomolded kayaks, approximately 17′ long. These must be launchable and retrievable safely while at sea, yet stowed solidly enough to withstand waves. Presumably, this translates into cradles on the amas.
Solar Panels
80 square feet of Solarex solar panels will be on board, split into two arrays that retract for safety in rough or windy conditions.
Antennas And Special Deck Fixtures
The Microship has quite a bit of on-board electronics, of course, and much of it is associated with space-consuming deck hardware that has to be accommodated in rigging design. This includes the radar dome, Qualcomm satellite antenna, video turret, GPS antenna, wind generator, and a large number of other antennas that must not interact with each other or affect safety. (The extensive array of computing and communication equipment is detailed in other documents.)
Power And Propulsion
Instead of a standard outboard, we wish to use an electric thruster. This can be powered by the batteries for short periods, directly driven by sunlight at about 1 hp, or operated at 6-7 hp in hybrid mode using the 6kw diesel generator (the last-ditch, noisy, but potentially lifesaving fallback position). In general, we prefer quiet, non-polluting operation using natural power sources including stored wind/solar energy.
High WQ; Art And Engineering
Finally, it is important that this be a balanced integration of art and engineering. The nature of this project involves extensive media, sponsor, and public contact — the Microship must be beautiful and well integrated, not a bunch of gizmology kluged onto an old tub. High-WQ (Weirdness Quotient) is important as well, but cannot be gratuitous: the system can and should look bizarre, but only in the elegant way that bespeaks novel solutions to design problems. WQ for the sake of WQ is a disaster, and must be avoided at all costs.
Well, there we have it. Let’s translate this into a floating substrate and start integrating all these systems so we can get Out There where we belong!