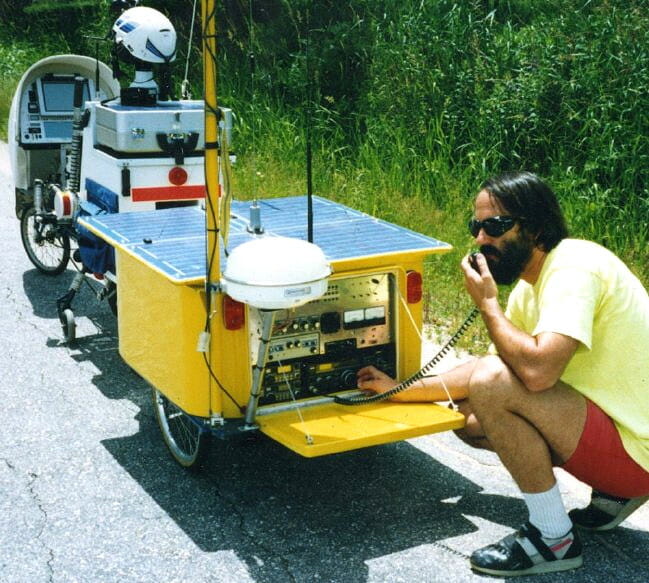
Bikelab Report #1 – BEHEMOTH Intro, HF Dipole, and Microwave Motion Sensor
While I was living at Sun Microsystems during the home stretch of the 3-year BEHEMOTH project, I started a publication series called the Bikelab Notes. Seventeen of these were published, and they carry some of the best technical details about the machine (since later media coverage was typically in the form of overviews slanted to the publication’s target market). These reports, written from the trenches of this gonzo engineering project, tend to be much more gritty and detailed… kind of like the Nomadness Reports that reflect the boat development work 20 years down the road.
Back then, email delivery didn’t allow for such niceties as photos… so as I move them into this collection I am adding scans of related images and other graphics where possible. Each post carries the date of its original publication, so they fold into the timeline of the library as if this were one huge 40-year-long blog.
Here is a note I sent out to folks in engineering at Sun (thanks to Don Hopkins for saving it all these years):
Hi…
Are you interested in ongoing reports from the bikelab here at Sun? I am working around-the-clock on BEHEMOTH (the successor to the 16,000-mile-old Winnebiko), a 350-pound recumbent bicycle with satellite earth station, GPS satnav, handlebar keyboard with humb mouse, ultrasonic head mouse, SPARC IPC for CAD and mapping and file-serving, Hypertalk user interface to the trio of FORTH real-time systems, heads-up display on the PC LAN, biketop publishing environment, complete ham radio station, micro security sensors, 54 speeds, regenerative and hydraulic braking, refrigeration and active helmet cooling system, speech synthesis and recognition, audio crosspoint network, MIDI, CDROM drive, 82 watts of solar panels, amateur television station, portable R&D lab, RF packet data link between manpack and bike, stereo, extensive camping gear, and so on.
Sun has become a major sponsor, providing workspace and facilities here on the Mt. View campus, and my job is to disseminate diverse information on bizarre human interfaces, portability, packaging, wireless networking, and the underlying nomadness that has kept the whole project alive for 7 years.
To facilitate publication of technical reports on the project, I have started an alias called Nomadness. If you’d like to receive ongoing updates, subscribe by sending a note to: no***************@*****ab.Corp
Thanks, and cheers from the unixycle lab!
Steve Roberts N4RVE
Here is Issue #1 of the series. (The photo above was taken several months after this article was written)
Bikelab Notes #1
December 9, 1990
©1990, 2011 by Steven K. Roberts
Brief Overview of the BEHEMOTH Project
I had great dreams of starting this series with a complete description of the new bike system, now renamed from Winnebiko to BEHEMOTH (Big Electronic Human-Energized Machine… Only Too Heavy). But the last time I wrote an overview, the file exceeded 50K.
As you probably already know, BEHEMOTH is a computerized recumbent bicycle that is getting completely out of hand. It’s about 350 pounds fully loaded, carries a whole suite of networked computers, and provides extensive radio communications ranging from a robust ham shack to cellular phone modem and satcom. It has a heads-up display, binary handlebar keyboard, and speech I/O. It uses GPS satellite navigation for mapping and the highest level of security response. It is becoming a unixycle, with an embedded SPARCstation for mapping, CAD, and file serving. The GUI is implemented in a Mac Portable on the console, driving a trio of FORTH 68CH11s. There’s a Peltier refrigerator, linked by a fluid loop to a heat exchanger in the helmet for body cooling. Power is provided by 82 watts of solar panels, and a regenerative braking system. It has something like 330 Meg of hard disk and at least 20 meg of RAM. And so on.
This project is obviously driven by passion, a recurring theme. It’s a blend of obsessions technoid and otherwise — and has been going on for 7 years. I’ve already pedaled about 16,000 miles around the US, and my tires itch violently… I’ll be back on the road full time in July, starting in western Iowa with the famed RAGBRAI madness (10,000 people pedaling across the state) and then continuing on from there, somewhere…
About 130 sponsors are making the whole thing possible, along with help from a wide variety of wizards, techies, machinists, engineers, gurus, friends, and consultants. In a sense, I am only project coordinator, though I do end up soldering into the wee hours, coding, fiberglassing, hacking, staring at the wall, piloting the CAD system, fashioning widgets, cussing at the greasier jobs, and eventually, I hope, pedaling. The point is that these updates should not be viewed as the techno-boasting of a solo inventor, but instead as a succession of reports on what this whole crazy industry can accomplish when the objective is high-tech adventure and the bottom line is pure, non-competitive FUN (though there may be a few commercial spinoffs). I will also give hard technical data and access to vendors wherever appropriate.
So. Rather than maunder on for the next hour trying to give you a complete description of the system, I’ll establish the pattern of this series up front: focused commentary on whatever I happen to be working on at the moment, followed (beginning in July) by tales from the road. But first, I suppose I should mention the basic design spec:
BEHEMOTH, whether moving or parked, must provide maximum possible autonomy in power generation, computation capability, file storage, communication, navigation, and maintainability — anywhere in the world, all controlled via a flexible graphic user interface. It must also be an elegant blend of art and engineering… and very comfy to ride.
On with this week’s details…
Bicycle-mobile HF Dipole Antenna
If you’re into ham radio and have ever operated mobile, you know that it’s not quite the same as flinging textbook-perfect wire dipoles into the trees or erecting a beam on a tall tower. There are all kinds of variables: imperfect grounds, effects of nearby objects, vehicle noise, impedance changes from wind-driven wiggling, etc. Move to a bicycle and it gets even worse: there’s not much of a counterpoise to work with, making the SWR of a normal vertical whip at anything lower than 15 meters unacceptable.
I use a half-wave Larsen antenna for 2 meters, and will build stacked J-poles for the Microsats. But the HF problem has bugged me for quite a while. Stopping to erect wire dipoles works, but eliminates the fun of mobile operation. Restricting activity to the high bands is unacceptable. Making an effective ground plane, even on a BIG bicycle like this, is impossible. And the spectre of RF dancing around in my microprocessors was almost enough to make me scrap the whole idea.
The solution is an antenna that does not depend upon an external ground. This boiled down to two choices: a dipole or a loop. The loop I tried is really quite an astonishing product — the AEA IsoLoop, available for about $350 from Amateur Electronic Supply or direct from AEA [no longer available, but well-explained over here, and a similar unit from MFJ is on the market]. It is about 32″ across, and carries a big black enclosure that houses an open-air variable capacitor driven by a stepper motor. This is controlled from the shack via a little box (which could easily be hacked to run under software control), and requires constant vigilance since tuning is VERY narrow. But performance is dramatic — I’ve had the IsoLoop outshine a wire dipole on some bands, even when mounted only 10 feet off the ground. This is an ideal choice for an attic antenna or someone with seriously limited space, but packaging constraints on the bike made it impossible for me.
The dipole made of HF whips makes a lot of sense, and my first experiments were with a whole thicket of Hustlers, using the shortened MO-4 mast and a little $8 steel dipole bracket from Burk Electronics. The Hustlers are notably broader band than the IsoLoop, but do require accurate physical changes of tip rod position whenever retuning is necessary (as well as resonator changes between bands). Though I maintained an effective sked for some time with these, the packaging problem got me again: the complete system for 80-10 meters required 14 resonators as well as the two masts. The back of the trailer would look like a quiver…
It looks like I have found the solution, however, and yesterday morning’s tests pretty well convinced me. The antenna of choice is the Outbacker, made in Australia and available in the US via Outbacker Antenna Sales. This odd-looking thing is a brightly-colored fiberglass lance, either 4 or 6 feet long (mine are 4, the “Jr.” model), studded with 8 female banana jacks in streamlined nacelles. There is a “wander lead” that begins near the base, is coiled counterclockwise around the body, and is plugged into the socket for the band you want.
This sounds arcane, but is really quite elegant. I took two of the all-band 4-foot units and mounted them as a dipole atop the BYP (Big Yellow Pole) that rises from the back of the trailer (this is nominally 6 feet long, but can be extended to 12 when conditions permit). No tuner or balun is required — I just drive the array directly from my Icom 725 transceiver. And performance is unmistakably HOT: band changing is easy, bandwidth is quite acceptable with only occasional tweaks of the tip rods, and overall weight is minimal (sorry, I don’t have a scale). This morning’s tests in the Sun MTV-4 parking lot yielded QSOs with 17 states and two provinces on 10 meters (mostly east coast), as well as easy voice and code chats on 12, 15, and 40. On 10 meters, anyone I could hear could also hear me, and signal reports were symmetrical even if they were relatively big guns. I was running 50 watts from the bike’s solar panels with the micro-dipole up 12 feet… and all in all, the experience was every bit as gratifying as ham radio should be.
A future article in this series will detail the mounting scheme that will let the Outbackers and the stacked J-poles fold out from a tight cluster on the BYP. Ham radio is becoming a very large part of this project, and a lot of the system engineering is devoted to making it effective in a variety of environments. You’ll be hearing more about all this as the weeks pass. (N4RVE here, by the way, pleased to meetcha!)
Microwave Security Sensor
One of the most common questions I hear about the bike, now worth somewhere near $1 million, is: “Mah gawd, man, how do you LOCK that thing?”
Well, I do have a cable lock, but it is seldom used. Instead, there is a very robust security system that includes 7 levels of sensors, opens voice and data links to my backpack during an alert, and even beacons latitude and longitude on ham packet frequencies if the Trimble GPS satellite navigation receiver starts reporting changes in coordinates without the right password. It can lock its own wheel, call 911 and deliver a synthesized message if it thinks it’s being stolen, and even do a few things I probably shouldn’t write about. Like ham radio, security is a complex subsystem that will appear in these reports often.

The most recent security project involved the level-1 sensor — a microwave doppler motion detector made by Alpha Industries. The model number is MSM10200, available direct as a developer’s kit for $195. With a power drain of only 10 mA from a 10-26V source, this device provides a closure to ground in response to movement within its field of view (which depends on choice of antenna — two come with the unit). Four trimpots let you set sensitivity and other operating characteristics… and coverage of an unobstructed area out to 100 feet or more is no problem.
The motion sensor is very sensitive, but there was one catch. I want BEHEMOTH to know when someone has moved within 8-10 feet. This is not necessarily an alarm condition (consider a restaurant parking lot), but it can be… or it may simply help eliminate falsing of other sensors due to wind or rumbling trucks. So how do we take a narrow 10 GHz microwave beam and turn it into a tight 360 degree pattern that surrounds a 12-foot-long bicycle?
Behind the seat of the recumbent, there is an area known as the RUMP (Rear Unit of Many Purposes). This is reasonably central, including the trailer, and also one of the highest points on the bike. The sensor is mounted inside the RUMP, with its feedhorn pointing straight up through a PVC fitting designed to interface a gutter downspout with 4″ pipe. This penetrates the fiberglass body, with a good seal to keep water out of other electronics in the enclosure.
Glued into the downspout part is a PVC 4″-to-2″ adapter, and inside that there is a copper cone made from Micaply (thin flexible PC board material). The cross-section of the cone is 90 degrees, and its apex is roughly even with the exit aperture of the microwave feedhorn. Atop all this is a 2″ cap, carrying the 7″ yellow barricade flasher (see future story on the lighting system).
Outdoor tests last week demonstrated that I got lucky (working with microwaves involves either great expertise on the subject — which I lack — or a healthy dose of luck). The radiation pattern appears to extend 360 degrees from the RUMP, spreading 24 degrees on either side of a horizontal plane even with the top of the seat. I was unable to get close enough to the bike to touch it without being noticed.
This output will be available to the RUMP Control Processor (one of the New Micros 68HC11 FORTH machines that handle all the real-time control) along with the UNGO system, optical sensors on all access panels, and various other inputs. The action taken in response to an alert depends entirely on software, and will be the subject of a future story…
I hate to stop, but there will be plenty of other opportunities to do this. No sense burning out on issue #1. Next week, I’ll tell you about making bicycle taillights out of high-brightness LEDs, a non-trivial task that was well worth the effort.
You must be logged in to post a comment.