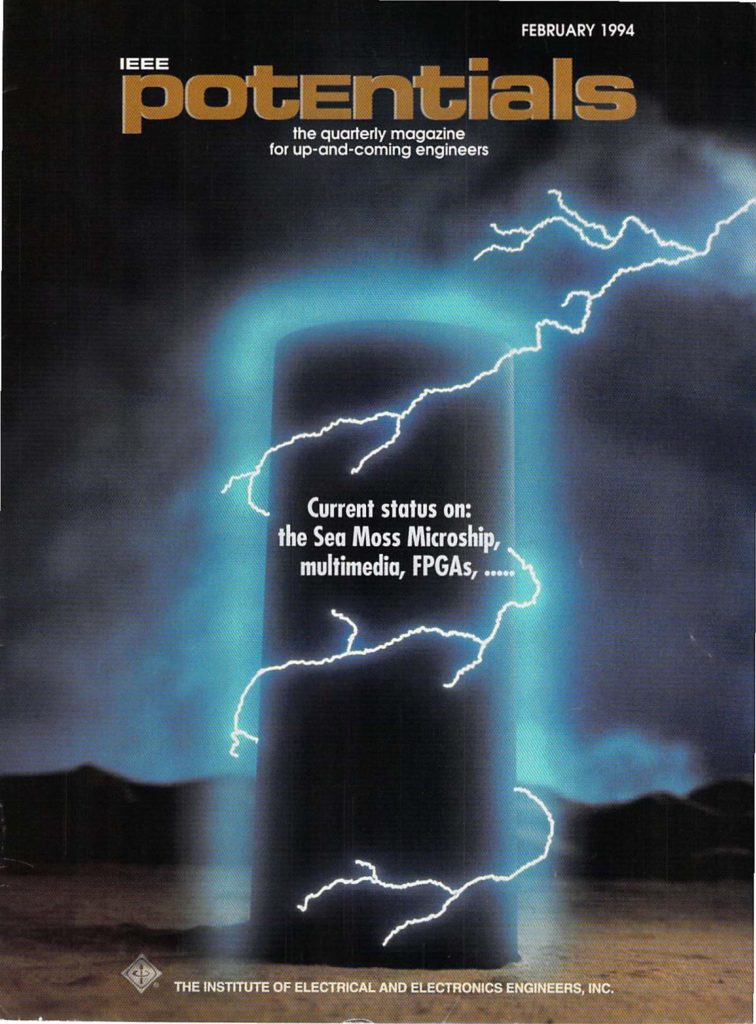
Sea Moss Microship – IEEE Potentials
This article was the first substantial published description of Microship design, kicking off a decade of development. The wide-ranging text describes the trimaran hull and mechanical structures, operating modes, embedded controls, data collection, productivity systems, audio/video tools including crosspoint switching, radio communications, networking, power generation and management, harsh-environment packaging, and life support. This was the development context for teams of engineering students during the two years the project was hosted at UCSD.
by Steven K. Roberts
IEEE Potentials
February, 1994
The Microship extends the design principles of BEHEMOTH (see box) which defined very loosely is a human/solar powered mobile workstation designed to render my physical location irrelevant. The new project is an aquatic version of this, significantly updated to represent the capabilities of 1993-1995 technology. Currently, I have moved into a lab at the University of California, San Diego, and a shop at the Scripps Institution of Oceanography, institutions that are jointly hosting the project. With the help of Scripps oceanographers, UCSD engineering faculty, a team of students from multiple departments, and over 100 industry partners and sponsors, I will bring the Microship project to fruition — then launch in 1995 for a few years of open-ended adventure linked to the network more tightly than ever before.
Much of this connectivity is devoted to the original objective of maintaining stable publishing and personal relationships while traveling full-time. This is no small matter: most serious travelers report loneliness, inability to remain current with news and industry developments, poor productivity, and homesickness as serious side-effects of being on the move. I have already solved these problems by depending on the network connections to move my perception of stability into “Dataspace,” and the new project will extend this metaphor by radically increasing both communication channel bandwidth and the sophistication of front-end software tools.
But new motives have surfaced as well. The Microship will carry a suite of environmental data collection sensors, and will transmit telemetry blocks via the Internet to schools, an Internet ftp server, and BEHEMOTH in its new home at the Computer History Museum. While I am not pretending to perform any kind of comprehensive survey, this will nevertheless yield interesting data for education, with potential spin-offs in the form of RF-linked data collection packages useful for local analysis of environmental conditions.
The remainder of this document describes the current state of Microship design…
Hull and mechanical
After exploring a number of configurations and brainstorming with naval architects, kayak designers, sailors, and mechanical engineers. Microship’s overall design has stabilized into a human/solar/sail-propelled trimaran — now being designed with the help of Nelson/Marek Yacht Design, a team of UCSD students, and the San Diego Supercomputer Center. It consists of three hulls — a custom center hull with 28-30 feet LOA and 4 feet beam, and two sleek double kayaks (about 22 feet LOA and 30 inches beam) for the amas, or outriggers. These are linked by retractable Solarex photovoltaic arrays laminated onto a Nida-Core (polypropylene honeycomb) structure, totaling 720 watts or about one horsepower of capacity in full sun. They occupy 4 feet x 10 feet of space on each side plus packaging overhead. If you envision a long narrow sailboat with aircraft cockpit carrying color computer/video/radar screens… joined to a pair of sea kayaks by a couple of folding solar oversize ping-pong tables resting on articulated arms that can also sprout wheels for trailering… then you have a rough idea of the general plan. (Disclaimer: this is still subject to change, and will probably evolve considerably from this description.)
Numerous hatches and sealed equipment bays in all hulls provide adequate space for packs, comm/nav gear, desalinator and water tank, food storage, tools, and so forth. Given the stresses encountered in rough seas and trailering, the composite layup will be considerably stronger than that of a normal lightweight kayak (possibly vacuum-bagged epoxy cylinder-molded compounded ply) with special attention paid to stress transition areas surrounding the attachment points for the retractable beam assemblies. These coincide with the bulkheads that separate the center hull into three segments, each about 10 feet long:
- Bow segment: The forward segment is isolated from the rest of the boat by a sealed bulkhead, since this is the region most likely to suffer hull-damage in a collision. This area is expected to be relatively wet, and will contain anchor, sail locker, environmental data collection, water processing, a shower stall, sprout garden, solar still, folding bicycle storage, and so forth. The deck will carry antennas, an access hatch, anchoring fixtures, and the bowsprit/pulpit.
- Cockpit module: My home on the water is the center segment. The cockpit itself occupies the aftmost four feet of this, containing a comfortable seat (with head below), hatches, rudder controls, bilge pump, console, communication gear, and so forth. (The keyboard desk flips out from under the console.) To get at the equipment racks and storage bays. I’ll have to crawl below the console into the engineering section, which contains two six-foot long, three-foot high, and one-foot deep equipment racks (which may, for packaging convenience, be segmented into 19-inch wide bays… there’s one in the bike trailer). This region is below an extended cuddy cabin, providing comfortable headroom and good lighting for seated work; a fold-down tabletop and stool provide the workspace. This is Microship’s lab, chartroom, emergency bunk, and hiding place for truly nasty weather. A bimini cover (a sort of convertible top) will protect me from sun and rain while in the cockpit, and a sliding hard cover provides security and storm defense.
- Cabin/crew module: Accessible either from the deck or through the bulkhead separating it from the Cockpit, is the sleeping cabin — a four by seven-foot bed with both aft and under-floor storage compartments. Parts of the bed fold into a seat, however, converting the cabin into a crew module complete with auxiliary control console, bimini, and manual access to sail and rudder controls. It has not yet been decided whether a flared section well above waterline will make this into a commodious living space, or if we should keep it as small as possible.
A few words should be said here about the brutal trade-off between comfort and light weight. In a boat, light weight is a good thing: it makes everything easier and faster. Yet, human comfort calls for spaciousness, storage room for espresso machine and blender, nice shower, bed…
Somewhere along the way, what began as a kayak project became a micro-yacht: partly from the realization that a kayak is a vehicle, not an aquatic life-support system. But anything called a “yacht” is too big, too hard to haul out or recover from capsize, and, frankly, too normal. The system described here is the evolving product of agonizing trade-offs and compromises.
Continuing with the overall hull design, this flexible trimaran architecture offers a number of features and operating modes:
- Stable. The boat will be extremely stable, allowing easy movement among hatches and cockpits. In a kayak, retrieving gear from a hatch is a risky operation — this trimaran will be more like a floating platform. Controlled flexion in the outrigger arms will prevent excessive stress in rough seas. Effective dihedral will be controlled by a floodable ballast tank.
- Compressed. To fit into berths and between narrowly spaced bridge supports, the solar structures can be “accordioned” and the hulls juxtaposed by retracting the outriggers, yielding an eight-foot beam.
- Water bivouac. Conditions may force alternative overnight accommodations: the solar surfaces will be backed by a composite honeycomb panel strong enough to support human weight. Two rectangular dome tents will fit on these surfaces, linked by a “hallway” covering the main console area; the berth in the aft-most hull segment provides more secure quarters for conditions when the wind loading of tents would be dangerous.
- Storm. In heavy weather, there is reason to be concerned about large flat surfaces, especially when heavy swells can momentarily close off one end and create a high-pressure air pocket. The solar panels will fold independently of the outrigger support structure to minimize the impact of wind, dumping seas, or peaking waves from below.
- Base camp. With its shallow draft and high molecular weight polyethylene hull bottom sheathing, the boat will be well suited to beach camping — when the two kayaks can be disconnected to provide seaworthy vehicles for local exploration or errands.
- Emergency dinghy. The flexibility of this design allows either kayak to be disconnected at sea and paddled ashore for a surf landing (or used for escape in the event of catastrophic damage to the main hull). In surf conditions dangerous to a multihull, all components can be disconnected, linked by lines, and hauled in after the main hull is surfed to shore. (The honeycomb-backed solar panels will float.) This spectacle is reserved for emergencies only….
- Road. Finally, the realities of full-time nomadics dictate frequent visits to companies and host sites. The three hulls will nest in a triangle, with retractable wheels and a bowsprit hitch to allow towing behind a vehicle.
The main hull will have a custom deck plan, though the amas will be more or less standard with the exception of pedaling stations, outrigger-support fixtures and custom segmentation to accommodate 10-foot spacing between the arms. In front of the main cockpit, a raised console (pressurized to protect the electronics from sea water incursion) will carry Mac, PC, video, radar, and control system LCDs behind a single Lexan window, with panels nearby carrying HF, Marine VHF, and a small cluster of switches and status displays. The bulk of the electronics will be in sealed pressurized hatches accessible through the companionway in the center hull segment, communicating with the console systems via the on board network. Other major deck fixtures include: whip antennas, radomes for the satellite earth station and marine radar, GPS antenna, a glass video turret, speakers, lights, drogue, compass, and the usual suite of survival and safety features such as grablines and cleats.
Propulsion is based on three power sources. First, on sunny days, the 720-watt solar array will provide approximately 50 pounds of thrust from a resting state, yielding cruising speed ambitiously estimated in the 4-5 knot range via thrusters deployed from the stern of each kayak. We are considering embedding integrated pedals in both of the kayaks to allow use as a human-powered craft. This mode could also be used for emergency propulsion of the entire vessel as well as battery charging from human or sail power.
Finally, a sail rig can be deployed to allow conventional wind propulsion — either a roller-furling Tedlar main on an unstayed carbon-fiber mast or a sloop rig that’s much more efficient but requires stays and greater complexity. If we do use a single main, tacking difficulties may be avoided by adding a retractable bow rudder to actively drive the bow through the wind (and allow CLR fine-tuning). Also, the loose foot is no problem since we can sheet it to a traveler running between amas. Details of the sail rig are currently under study — roller furling main implies an aerodynamically non-optimal spar, so that may not be the best choice. This is an area rife with even more trade-offs than most!
Electronics packaging will depend heavily upon a few tricks to minimize the impact of the fiercely corrosive sea water environment (dubbed “aqua regia” by some). The control console and main equipment bays will operate at about three psi above ambient, provided by a small electric pump (with a Schrader valve for manual bicycle-pump backup) followed by a desiccant cartridge and fine-mesh filter. The intent here is to prevent the enclosures from thermally breathing moist, salt-laden air in the event of a leak. They will outgas and sound an alarm when the control system notices a pressure drop uncorrected with a temperature change. Eventually the desiccant will become saturated, and I’ll dry it over the camp stove.
Related packaging issues affect every part of the design, and we will make liberal use of undersea connectors, sealed or potted subassemblies, and a mineral-oil bath for components that need to be serviceable but don’t justify inclusion in the pressurization system. (One of the nice things about working with oceanographers at Scripps is that they have already developed effective solutions to these problems.)
Computer systems and applications
This area involves extensive detail, but for purposes of this overview I will keep it at the summary level. Basically, there are two classes of computers on board: the high-level systems and the low-level control network.
At the high level, the primary system will be a repackaged Macintosh PowerBook with color active-matrix screen (possibly the 180C). The keyboard and a sealed pointing device will provide text entry and cursor control, and Digital Ocean’s wireless spread-spectrum AppleTalk link will connect Microship computers to the one in my backpack and to other boats in the possible technomadic flotilla. The second cockpit may contain a Mac as well to support the work of my traveling companion.
Macintosh applications include: Eudora for electronic mail (via cellular phone and satellite), networking tools, Word for text and publications, a database manager linked to maps and navigation charts via GeoQuery, project planning tools, AutoCAD, navigation and charting, language training, and demo software. This system, like its counterpart on BEHEMOTH, will be my home operating environment and link to the world. However, it may be assisted by a similarly scaled PC to handle navigation tasks without requiring context switching out of my writing and communication tools.
Unlike BEHEMOTH, the Macintosh will not be essential to the operation of the low-level control system. On the bike, I did this to present a graphic user interface (HyperTalk layered atop FORTH). Also, although the Mac will still allow a pleasant work environment for all levels of the Microship system, it will not be required for basic operation. (Even though it would reduce console real-estate by eliminating a second screen, using the Mac as the front-end for continuous-duty control negatively impacts the power budget, increases complexity, and introduces dangerous single-point failure potential in a critical survival area.) Instead, a Sharp color LCD (that also accepts NTSC video) will be managed by an Ampro-based PC-104 system atop the control network, yielding a continuous display of navigation, safety, status, and environmental data:
- Latitude and longitude, waypoints, heading. & other navigation data
- Air and water temperatures
- Radiation, salinity, pH, turbidity, depth, and trim
- Equipment bay pressure and temperature
- Barometric pressure, with trend data
- Time of day and stopwatch
- Battery status and estimated time-to-full or time-to-empty
- Power control map, local bus voltages, load and charge currents
- Drinking water level and desalinator status
- Security system status and self-test
- Propulsion system performance and load-share
- Marine radar detected
- Communication system virtual front panel
- Processor and control system self-diagnostics
- Stress, vibration, and other physical system parameters
One of the design characteristics that made BEHEMOTH rather too complex was the presence of three separate equipment bays (console, RUMP, and trailer). Each imposed considerable overhead in terms of shock-isolated packaging, power distribution, local control, cabling, and audio/serial networking. While the resulting design is architecturally fascinating, the system is intimidating in scope and documentation is a nightmare.
The Microship will be much simpler, with only one main equipment bay and one straightforward network of microcontrollers. A single power distribution bus will suffice for all. All audio will be routed through one of the crosspoint boards developed for BEHEMOTH (supported by a dedicated micro-server), and random serial communications will be handled likewise.
The low-level control network consists of about 15 remote New Micros FORTH 68HC11 processors, lined via the Easy-A multidrop bus to a single hub that supports the display screen and can be addressed directly by the console keyboard. These little processors handle power management, propulsion control, environmental data collection, diagnostics, security, keyboard steering, audio networking, transceiver front-ends, navigation sensors, event scheduling, and other essential details.
(photo essay of Microship electronics developed over the next 2 years)
Speaking of user interface, this project will again differ significantly from its predecessor. Since I no longer have handlebar constraints, I’m using a waterproof QWERTY keyboard from Paravant, mounted on a flip-up console that retracts under the cuddy/console when not in use. This is faster and simpler to use, and if packaging constraints permit, is preferable to the chording scheme with which I have grown familiar. Cursor control will no longer be an ultrasonic head mouse, since I have no intention of wearing a helmet (brain interface unit) while on the water. We are currently working with the Interlink DuraPoint, which is completely sealed. Both keyboard and pointing device can be steered to PC or Mac systems via the “Keystone” from Silicon Valley Bus Company.
Communications
As with BEHEMOTH, the communication links to the outside world are critical—even more so, given the survival issues associated with being on the water. In addition to the EPIRB for life-threatening emergencies, the Microship will carry a full ham radio station, marine VHF and HF, satellite e-mail terminal, cellular phone with modem and fax, security pager, and voice and data links to the backpacks of both crew. Additionally, new wireless mail services arc severing the ties even further and will be explored as they become available.
The Internet connection is central to the success of this project: Dataspace is my hometown, allowing me to maintain a suite of business and personal relationships absolutely independent of physical location.
The high-reliability mail path is via the Qualcomm OmniTRACS terminal, a KU-band uplink to the GSTAR satellite. This acquires and then tracks the geosynchronous bird even while the Microship is in motion. Extensive custom software (written for the BEHEMOTH project by Qualcomm) allows it to appear to the Mac’s mail system (Eudora) as a transport medium, passing messages to and from the Internet via a SPARCstation located at the satellite hub in San Diego. The system even stamps all outgoing messages with my latitude and longitude, which, although not as precise as the GPS navigation system, adds a level of comfort and security to open-water travel. A mapping program can display my location in real time (at the Computer Museum, my base office, Qualcomm, UCSD, Scripps, and other places).
This is a slow mail path, however, useful primarily for high-priority short messages. Longer transfers, such as manuscript file transmissions, JPEG images, and the day’s routine mail (typically 60-80 messages), will take place through a high-speed modem attached to the cellular phone, new wireless e- mail services, or a hardwired connection at a host’s site. Conveniently, both this and the satellite use the same mail program on the Macintosh, keeping the user interface consistent. The bike has a SPARC with PPP via cellular… a bicycle with an IP address! We’re adding a Tadpole SPARCbook to the ship as well to support more advanced net services than e-mail (while providing a local file server on the ship’s Ethernet).
The third data path is via ham radio — packet and other digital protocols. A widely supported RF-linked network is in place, offering reasonably high reliability for non-business or emergency traffic, with AMTOR and PACTOR allowing worldwide e-mail gateways to the internet via the on board Icom HF transceiver and multi-mode TNC. VHF packet is via a PacComm Handi-Packet, which will also allow control/security messaging via the backpack computer.
In addition to data communication, the Microship will be provided with extensive voice capability, with marine radio as well as HF, VHF, and UHF amateur equipment. A major design goal here is to have 100% probability of being to reach someone somewhere, at any time from anywhere. (The EPIRB should assure that with one flick of the switch, in an emergency, and the Microship will look like a five-alarm fire to the Coast Guard.)
Finally, security is very much a communications issue. Most of the responses to security violations (proximity, motion, shock, lat-long change without a password, unauthorized hatch access, and so on) involve some combination of paging me, transmitting help messages into the Net via satellite, or calling 911 via cellular phone and delivering an emergency voice message tagged with latitude-longitude information.
Power generation and management
With 720 watts of solar panels and some 300 watts of pedaling capacity split between two people, there is a significant resource-management issue here. Efficiency suggests running the array and thruster at 48 volts and then DC-DC converting that down to charge the main 12-volt system battery. However, simplicity may rule and dictate fat cables and high-current connectors. In any case, one of the FORTH microcontrollers will be dedicated to active management of power distribution, the percentage available for propulsion, and battery condition.
Power distribution throughout the Microship will be modeled exactly after BEHEMOTH: A battery bus (overload protected) runs to all sites, with local software-controlled FETs and switching regulators associated with each load. Manual switching to high-reliability loads, like bilge pump and lights, will be provided to prevent a software crash from becoming a life- threatening situation. A “JATO” mode will devote everything, including battery, to the thruster when I need to scoot out of the way of a freighter in the fog.
A continuous task on the power manager will be observation of battery status and prediction of time to full or empty based on observed performance. A graphic map of the power distribution system can also be displayed to aid in diagnostics and task planning, with some automatic load shedding to provide a graceful degradation of service as the battery level dips below normal levels.
Audio/video components
In the past, my primary tool for capturing and publishing the essence of this nomadic experience has been text—using the handlebar keyboard and on-board computers to write stories which were then transmitted electronically to publishers. On this next journey, I will add high-quality audio and video capability to allow pre-production of radio programs, publication of digitally transmitted still video frames, and capture of live video for later editing.
All this has to be smoothly integrated with the Microship system — fumbling below deck for the camcorder is unacceptable in the heat of battle. An audio recorder will be remote-controllable, with stereo microphone near the console, and miniature video cameras will be mounted in a glass turret on deck and on the radar arch. Beyond this. I don’t know the details… stay tuned!
As noted earlier, all audio is routed throughout the system via a software-controlled crosspoint matrix. This essentially allows anything to talk to anything — speech synthesizer, cellular phone, ham radio, MIDI system, entertainment audio, boom mic headset, marine radio, tape recorder, intercom to backpack, and so forth. Maximum generality is the key to the hardware design.
Safety and survival systems
Finally, there’s the matter of staying alive. This is much more of a challenge on the water than on the road, with one very significant threat (drunk drivers) replaced by another (drunk power-boaters). In addition to that, we have to deal with dehydration, drowning, hypothermia, cold shock, sharks, storms, surf landings, freighters in the dark, getting lost, hull damage from floating objects or coral reefs, sickness, clapotis, and williwaws.
No single technology can take care of all that, of course, but the Microship will be designed to maximize my chances of survival over the next few years. For visibility, strobe and bi-color LED marker lights will be built into the deck and mast, with BEHEMOTH-like LED taillights on the stern for land mode. A marine radar, probably Furuno’s compact LCD 1621 drawing only 30 watts, will let me see what’s out there. The usual flare/smoke/dye kit will facilitate rescue operations, and electronically-launched rockets (wax-sealed fireworks?) may be mounted in a small fixture to alert a rapidly-closing vessel to my low-profile existence if they’re ignoring my radar reflection, flashing lights, and urgent shouts on Channel 16.
A reverse-osmosis desalinization system will provide fresh drinking water, which not only keeps the human engine hydrated but also serves as the coolant for the helmet heat exchanger I currently use on the bike (from Life Support Systems). This can pull approximately 75 watts of waste heat from my body, minimizing performance derating under conditions of elevated ambient temperature. A backup fresh-water system in the form of a folding solar still will also be on board for emergencies (stowed in the forward hull segment).
Naturally, a full complement of wilderness camping gear, including cooking and medical supplies, will provide survival tools when I’m not in range of support facilities. This is expected to be a more frequent need in the Microship than it was on BEHEMOTH, since only in the wild west have I encountered situations where essential services are often out of pedaling range. On water, this will be much more common — with the worst-case scenario being the need to lie to a drogue off a lee shore and camp at sea in a storm. Water bivouac mode, as well as the ability to squirm down into the hull and under cover, should make this comfortably survivable, now that the originally planned kayak has become a kayacht!
Any discussion of safely has to include maintenance issues: a full repair kit, including glass/epoxy hull patching, electronic diagnostics, and basic mechanical tools will be aboard to keep everything running smoothly and, presumably, afloat.
Summary
This is just a snapshot of the project’s current status, and will be expanded considerably as work proceeds in The Nomadness Notes (free via Internet). As I mentioned earlier, I have established the laboratory at Scripps/UCSD and am now assembling a team of engineering students to work on the Microship as an interdisciplinary project platform. There are all sorts of things yet to be determined: autopilot design, rudder/thruster integration, network architecture, user interface, beam assembly design, the flexible-vs-rigid trade-off in outrigger structure, inventory of hand-held back-up equipment, and much more.
The Microship is now under construction on the UCSD campus (San Diego), with dozens of students involved in the project. For occasional updates, send mail to [obsolete address redacted] containing the single line: add nomadness
The command “help” will give you more information on the mailing list processor. Thanks for your interest, and cheers from the road…
About the author
Steven K. Roberts has been a high-tech nomad for 10 years. Before that, he owned a consulting business focusing on industrial control systems and published three textbooks on that and related subjects. His more recent book, Computing Across America, describes his first 10,000 miles of adventure, and subsequent writings are available free via Internet by ftp from ucsd.edu under /nomad. Steve welcomes suggestions, offers of help or hospitality, applications for crew positions, and other input via e-mail only: [obsolete address redacted]
BEHEMOTH
Nearly 10 years ago, I launched myself from Columbus, Ohio on what was expected to be an 18-month high-tech recumbent bicycle tour around the United States, linked to friends and publishers via online networks. What I did not anticipate was the resulting three-way symbiosis of sponsors, media, and the project itself: the original Winnebiko was rebuilt into the Winnebiko II in 1986, and then, after three and a half years of work in Silicon Valley with the help of 140 sponsors and some 45 volunteers, into the current system known as BEHEMOTH. This machine, estimated at $1.2 million, has covered over 17,000 miles around America (plus nearly 85,000 miles in trade show, media, and speaking tours, hauled inside a mobile lab known as the Mothership).
This has been a strangely successful enterprise, but it is time for change. Lured inexorably by water, I am now developing the Sea Moss Microship. This kayak-trimaran embodies the mission-critical subsystems of BEHEMOTH while optimized for the challenging environment of full-time aquatic adventure.
As the foregoing suggests, BEHEMOTH can be very loosely summarized as a human/solar-powered mobile workstation designed to render my physical location irrelevant. The bike is equipped with Mac, DOS, and SPARC environments, a satellite electronic mall link, cellular phone with modem and fax, handlebar chord keyboard and ultrasonic head mouse, helmet-mounted display, a complete ham radio station that includes digital modes, speech I/O, and much more, all controlled by a network of embedded FORTH processors and carried on a 105-speed custom recumbent bicycle pulling a solar-roofed trailer.
You must be logged in to post a comment.